在现代工业领域,飞轮作为能量存储和惯性稳定的关键部件,其性能直接影响着整个系统的可靠性和效率。特别是在高频工况下,飞轮面临的动平衡与抗震问题尤为突出,这对工程设计提出了严峻挑战。本文将围绕飞轮系统的动平衡与抗震协同设计方法展开深入探讨。
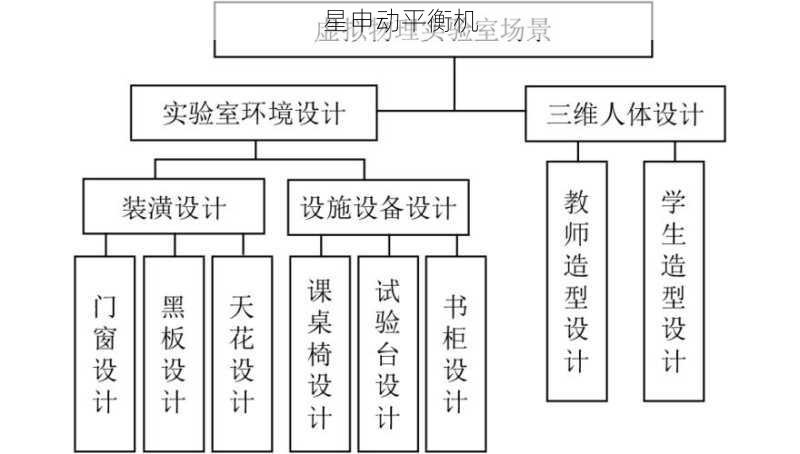
首先需要明确的是,高频工况下的飞轮系统面临着复杂的动力学环境。当转速达到每分钟数万转时,微小的质量偏心就会产生巨大的离心力。有实验数据显示,在30000rpm转速下,仅1克的质量偏心就能产生约1000N的不平衡力😮。这种动态载荷不仅会导致轴承过早失效,还可能引发灾难性的共振现象。
在传统设计方法中,动平衡与抗震设计往往是割裂进行的。工程师们通常会先进行动平衡设计,再单独考虑抗震性能。但这种做法存在明显缺陷:一是忽略了两种因素的耦合效应;二是可能导致设计过度保守,增加不必要的重量和成本。相比之下,协同设计方法具有显著优势👍。
协同设计的核心在于建立统一的分析模型。这个模型需要包含以下几个关键要素:1)飞轮转子的弹性变形特性;2)支承系统的刚度与阻尼特性;3)环境振动谱特征。通过有限元分析可以发现,在高频段(通常500Hz以上),飞轮本体的模态特性会显著影响系统的动态响应😯。这就意味着简单的刚性转子假设已不再适用。
具体到设计流程,建议采用以下步骤:首先进行多目标优化设计,将动平衡精度和抗震性能同时作为目标函数;其次采用主动平衡技术,通过实时监测和配重调整来补偿残余不平衡;最后进行环境振动试验验证,重点考察系统在扫频振动下的稳定性。
材料选择在协同设计中起着决定性作用。碳纤维复合材料因其优异的比强度和阻尼特性,已成为高速飞轮的首选材料。实验表明,采用[0/±45]铺层设计的碳纤维飞轮,其固有阻尼比可达0.015,是金属飞轮的3-5倍😲。这种特性使其在抑制振动方面具有天然优势。
支承系统的设计同样关键。磁悬浮轴承因其无接触特性,可以完全消除机械摩擦,特别适合高频应用。但需要注意的是,磁轴承的控制系统必须具有足够带宽来抑制高频扰动。研究表明,当控制带宽达到转子最高工作频率的5倍以上时,系统才能保持良好的稳定性📈。
在实际工程应用中,我们还需要考虑制造公差的影响。以某型卫星飞轮为例,其动平衡等级要求达到G1.0级(残余不平衡量小于1g·mm/kg)。要达到这个标准,不仅需要精密的加工设备,还要配合激光动平衡校正工艺。有趣的是,适当保留一定的柔性反而有利于抗震性能,这体现了刚柔并济的设计哲学🤔。
展望未来,飞轮动平衡与抗震协同设计将朝着智能化方向发展。基于数字孪生的实时监测系统可以预测飞轮的健康状态,机器学习算法能自动优化控制参数。这些新技术的应用,有望将飞轮系统的可靠性和寿命提升到一个新的高度🚀。
高频工况下的飞轮设计需要打破传统思维,采用多学科协同的方法。通过综合考虑动力学特性、材料性能和控制系统等因素,才能开发出既满足动平衡要求,又具备优异抗震性能的飞轮系统。这不仅是技术挑战,更是一种工程艺术的体现🎨。