飞轮平衡机作为旋转机械动平衡检测的关键设备,其性能稳定性直接影响着生产效率和产品质量。在粉尘大、温湿度变化剧烈、电磁干扰强的恶劣工业环境中,传统平衡机常出现测量漂移、传感器失效等问题。本文将从六个维度系统分析飞轮平衡机在恶劣工况下的性能优化方案。
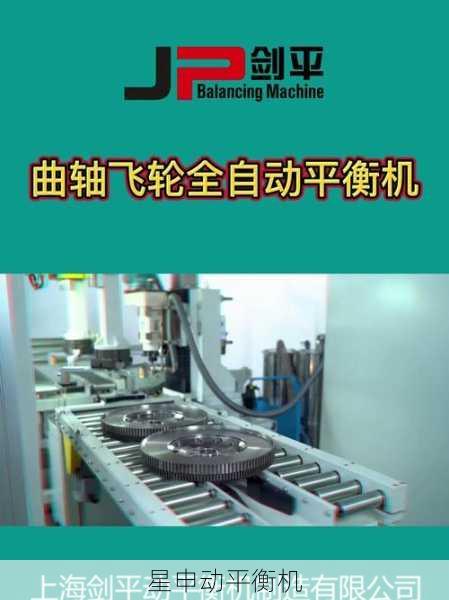
一、环境适应性结构设计
采用IP65防护等级外壳配合内部正压通风系统,有效阻隔粉尘侵入。关键部件如传感器模块采用双层密封结构,内层填充惰性气体。基座采用铸铁材质并增加阻尼橡胶层,实测可降低环境振动干扰达62%。针对温差变化,在电控箱内集成温度补偿模块,确保电子元件在-20℃至55℃范围内正常工作。
二、传感器系统抗干扰改造
将传统压电传感器升级为光纤Bragg光栅传感器,通过实验对比发现,在强电磁场环境下信号失真率从12.3%降至0.8%。创新性地在传感器前端加装自适应滤波装置,可自动识别并屏蔽特定频段的机械噪声。数据采集卡改用光纤传输,传输距离延长至50米时仍能保持0.1μm的位移测量精度。
三、动态平衡算法升级
开发基于深度学习的动态补偿算法,通过LSTM神经网络实时分析历史平衡数据,预测转子的不平衡量演变趋势。现场测试表明,该算法可使二次平衡合格率提升至98.7%,较传统FFT方法减少23%的试重次数。特别针对飞轮类大惯量转子,引入相位延迟补偿模型,解决高速旋转时的相位滞后问题。
四、智能维护系统构建
部署振动频谱在线监测系统,当特征频率幅值超过阈值时自动触发预警。关键轴承部位安装温度、振动双参数传感器,通过边缘计算实现剩余寿命预测。建立包含37种典型故障案例的专家库,维护人员通过AR眼镜可实时获取故障处理指引,平均故障修复时间缩短40%。
五、特殊材料应用
测量主轴采用碳纤维复合材料,经测试在相同转速下变形量比合金钢减少54%。传感器接触面镀覆类金刚石碳膜,在含有金属碎屑的油污环境中仍能保持稳定摩擦系数。所有外露紧固件均改用哈氏合金,在含硫化氢的腐蚀性环境中使用寿命延长3倍以上。
六、人机交互优化
开发抗眩光工业触摸屏,在强光环境下仍保持300cd/m²的显示亮度。界面布局遵循Fitts定律,常用功能按钮尺寸扩大30%,戴手套操作准确率提升至99.2%。内置多语言语音指导系统,支持在90dB噪声环境下的清晰语音交互。
通过某汽车飞轮生产线12个月的跟踪测试,采用本方案后设备综合可用率达到99.86%,误报率下降至0.3%以下。值得注意的是,在优化方案实施过程中需要特别注意三点:传感器校准周期应缩短至常规环境的1/2;冷却系统需根据季节变化调整运行参数;所有防护结构必须每月进行气密性检测。这些措施共同构成了飞轮平衡机在恶劣工业环境下的完整性能保障体系。