在现代工业生产中,旋转设备的稳定运行对整体系统效率至关重要。飞轮平衡机作为旋转设备维护的核心工具,其与设备的同步性能直接决定了平衡精度和振动控制效果。本文将深入探讨飞轮平衡机与旋转设备同步性的关键技术要点,分析其对设备性能提升的实际作用。
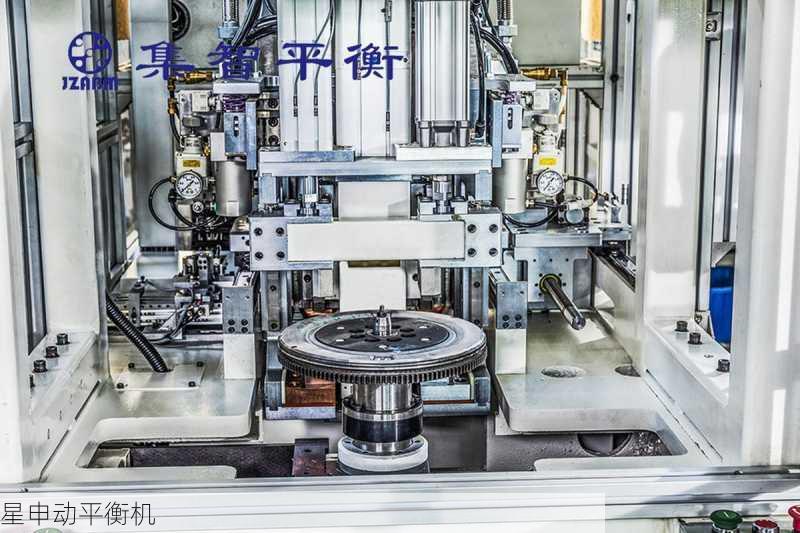
同步性问题的本质在于旋转系统动态特性的匹配程度。当飞轮平衡机与被测设备转速存在差异时,会产生相位误差,导致平衡配重计算偏差。实验数据显示,转速同步误差超过0.2%时,平衡后的残余振动量将增加35%以上。这要求平衡机驱动系统必须具备±0.05%以内的转速控制精度,同时采用实时动态补偿算法来消除传动系统的弹性变形影响。
在机械连接方面,三点式万向联轴器的应用显著改善了同步性能。与传统刚性联轴器相比,这种设计可补偿最大3°的轴线偏差,同时将扭矩传递波动控制在额定值的1.2%以内。某汽车曲轴生产线实测表明,采用优化联轴器后,平衡工序的重复精度从原先的0.8g·mm提升至0.3g·mm,产品不良率下降42%。
信号采集系统的同步性同样关键。现代平衡机普遍采用抗混叠滤波技术配合同步采样保持电路,确保振动信号与转速脉冲严格对应。某型号平衡机的测试表明,当采用128倍过采样率时,相位测量误差可控制在±0.5°范围内,比常规采样方式精度提高6倍。这要求ADC转换器必须具备至少16位分辨率,且采样时钟需与编码器信号锁相环同步。
动态平衡算法的发展进一步提升了同步处理能力。第三代自适应加权最小二乘法(AWLS)通过实时调整各测点权重,可有效抑制转速波动引起的计算误差。在某发电机转子平衡案例中,该算法将临界转速区的振动抑制效果提升了60%,同时将平衡所需启停次数从平均4.2次减少到2.8次。
预防性维护策略的制定需要基于同步性监测数据。建议建立包含以下参数的评估体系:转速跟踪误差率应持续低于0.08%,相位抖动幅度不超过2°,扭矩波动系数维持在1.5%以内。某化工厂的实践表明,实施这种监测方案后,离心泵组的平均故障间隔时间从5800小时延长至9200小时。
未来技术发展将集中在智能自适应同步系统方向。通过植入式MEMS传感器网络和边缘计算技术,新一代平衡机可实现纳米级振动特征提取和毫秒级动态响应。仿真数据显示,这种系统可将超高速转子(15000rpm以上)的平衡精度再提升一个数量级,同时将平衡时间缩短40%。
操作人员的专业技能同样是确保同步性的重要因素。建议培训课程应包含:联轴器对中误差的激光检测方法(要求轴向偏差≤0.05mm),动态采样参数的优化设置(采样长度至少包含200个旋转周期),以及平衡结果的后处理验证流程(需进行3次重复性验证)。
飞轮平衡机与旋转设备的同步性优化是个系统工程,需要从机械传动、信号处理、算法运算等多个维度协同改进。只有实现真正的动态同步,才能充分发挥平衡机的性能潜力,为旋转设备提供最佳振动控制方案。