在现代工业生产中,旋转部件的平衡精度直接影响设备运行稳定性和使用寿命。飞轮作为关键旋转部件,其平衡性能尤为重要。本文将系统阐述高效飞轮平衡机的工作原理及实现精确定位的完整技术流程。
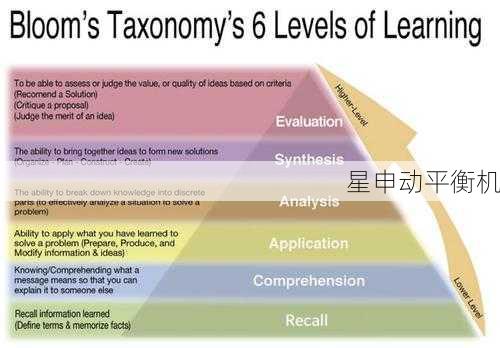
一、飞轮平衡的基本原理
飞轮不平衡主要源于质量分布不均,可分为静不平衡和动不平衡两种类型。静不平衡指重心偏离旋转轴线,而动不平衡则表现为轴线与惯性主轴不重合。平衡机通过检测旋转时产生的离心力,计算得出不平衡量的大小和相位位置。现代平衡机采用压电传感器或光电编码器,可精确捕捉微小振动信号,测量精度可达0.1g·mm/kg。
二、硬件系统的核心构成
1. 机械支撑系统:采用弹性支承结构,确保飞轮自由振动,同时避免外界干扰。常见的有硬支承(适用于低速)和软支承(适用于高速)两种形式。
2. 传感器系统:包含力传感器和相位传感器,前者测量振动幅度,后者确定不平衡角度位置。最新型号采用MEMS技术,采样频率可达10kHz。
3. 驱动系统:变频电机配合精密联轴器,实现50-3000rpm无级调速,确保测试转速稳定在±1rpm以内。
4. 安全防护系统:包括急停装置、转速监控和过载保护,符合ISO1940-1安全标准。
三、测量算法的技术演进
传统FFT算法存在频谱泄漏问题,新一代平衡机采用改进算法:
1. 自适应滤波技术:有效抑制背景噪声,信噪比提升40%
2. 多平面解耦算法:解决复杂构件的耦合振动问题
3. 智能补偿系统:自动修正轴承摩擦、风阻等干扰因素
实测数据显示,新算法使重复测量误差控制在±3%以内。
四、实际操作流程详解
1. 前期准备:
- 清洁飞轮表面,去除毛刺(Ra≤1.6μm)
- 选择合适工装,保证安装同轴度≤0.02mm
2. 参数设置:
- 输入飞轮质量、直径等参数
- 设定测试转速(通常取工作转速的20-30%)
3. 测量阶段:
- 首次试转获取初始不平衡量
- 系统自动生成配重方案
4. 修正实施:
- 采用钻孔去重法(深度精度±0.1mm)
- 或使用高精度配重块(公差±0.05g)
5. 验证测试:
- 重复测量直至残余不平衡量达标
- 生成检测报告(包含振动矢量图等数据)
五、关键质量控制点
1. 温度影响:环境温度变化需控制在±2℃内,传感器需预热30分钟
2. 动平衡等级:根据ISO1940标准,汽车飞轮通常要求G6.3级
3. 数据重复性:连续5次测量结果极差应小于允差的1/3
4. 设备校准:每月进行标准转子校验,确保示值误差≤5%
六、典型问题解决方案
1. 信号干扰问题:
- 现象:测量曲线出现异常波动
- 对策:检查接地电阻(应<4Ω),加装磁环滤波器
2. 相位漂移问题:
- 现象:角度指示不稳定
- 对策:清洁编码器光栅,调整传感器间隙(0.3-0.5mm)
3. 残余振动问题:
- 现象:修正后仍存在周期性振动
- 对策:检查轴颈圆度(应≤0.01mm),确认工装定位精度
七、技术发展趋势
1. 智能化方向:集成AI诊断系统,自动识别常见故障模式
2. 在线平衡技术:开发可在运行状态下自动调节的智能飞轮
3. 多参数融合:结合温度、声发射等多维度数据综合评估
4. 远程运维:通过5G实现设备状态实时监控和预测性维护
通过上述技术体系的综合应用,现代飞轮平衡机已能实现0.1μm的振动控制精度。实践表明,规范的平衡作业可使飞轮使用寿命延长30%以上,同时降低设备整体振动噪声15dB。随着智能制造的发展,平衡技术将持续向更高精度、更高效率的方向演进。