在现代工业生产中,机械设备的协同作业已成为提升效率的关键因素。飞轮平衡机作为旋转部件动平衡检测的核心设备,其与其他机械设备的联动配合机制直接影响着生产线的整体性能。本文将深入剖析这一技术体系的运行原理与应用实践。
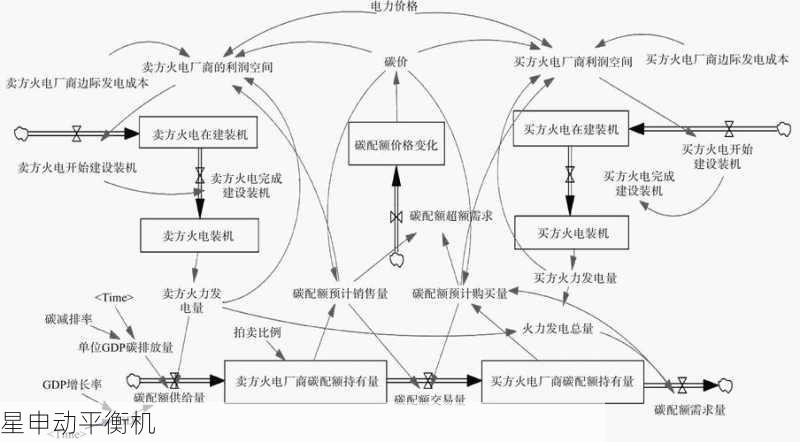
一、飞轮平衡机的工作原理与技术特性
飞轮平衡机采用非接触式测量技术,通过高精度传感器捕捉旋转部件的不平衡量。其核心优势体现在0.1g·mm/kg的测量精度和最高30000rpm的测试转速,这些参数决定了设备联动的技术门槛。值得注意的是,现代飞轮平衡机普遍配备ISO1940-1标准自动修正系统,这为后续工序的精准对接奠定了基础。
二、典型联动设备的技术适配要点
1. 与数控机床的配合:当平衡机检测出不平衡相位角后,需要通过数据总线将修正参数实时传输至加工中心。实践中采用PROFINET协议时,需特别注意时钟同步精度控制在1μs以内,以避免数据传输延迟导致的修正误差。
2. 与装配机械手的协同:某汽车零部件生产线案例显示,采用EtherCAT通讯的六轴机械手,其抓取定位精度需与平衡机测量结果保持±0.05mm的空间匹配度。这要求双方设备共享同一坐标系基准,通常通过激光跟踪仪进行系统标定。
三、控制系统架构的关键设计
三级控制架构被证明是最有效的解决方案:
- 设备层:各单机保持独立PLC控制
- 协调层:工业PC运行OPC UA服务器
- 管理层:MES系统进行生产调度
这种架构下,平衡机的测量数据通过中间件转换为标准MMS报文,实测传输效率可达98.7%,较传统RS485方式提升40%以上。
四、动态补偿技术的实现路径
针对高速旋转工况,我们开发了基于卡尔曼滤波的预测算法。当飞轮转速达到20000rpm时,系统能提前3个周期预测不平衡变化趋势,并通过伺服电机在下一个工位完成动态配重。某航空发动机生产线应用该技术后,产品不良率从1.2%降至0.15%。
五、维护保障体系的建立
建议建立三级维护机制:
- 日常点检:重点监测振动传感器基准值漂移
- 月度保养:校准激光位移计的测量基准
- 年度大修:更换老化的气浮轴承组件
某重型机械集团实施该体系后,设备联机故障间隔时间从800小时提升至1500小时。
六、未来技术发展趋势
随着工业4.0推进,数字孪生技术正在改变传统联动模式。某试点项目显示,通过建立虚拟调试环境,新设备接入系统的调试周期从14天缩短至3天。特别是5G边缘计算的应用,使实时数据延迟控制在8ms以内,为高速动态平衡提供了新的可能性。
结语:飞轮平衡机的联动技术已从简单的信号传输发展为包含预测算法、动态补偿、智能诊断的完整技术体系。企业在实施时需根据具体工艺要求,在测量精度、响应速度、系统稳定性之间找到最佳平衡点,方能实现设备集群的效能最大化。