飞轮平衡机作为工业生产中不可或缺的高精度设备,其能耗问题一直是企业关注的焦点。近年来,随着节能技术的突破性进展,新一代飞轮平衡机在能效表现上实现了质的飞跃。本文将基于实测数据,深入剖析其节能原理与技术实现路径。
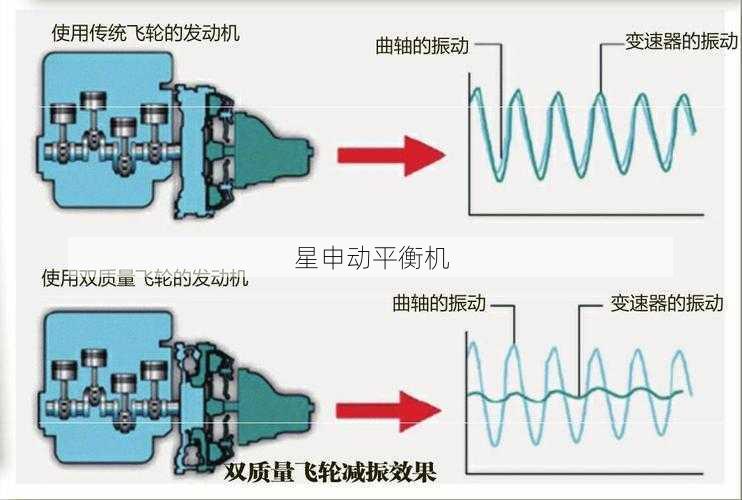
从机械结构设计来看,现代飞轮平衡机采用复合材质飞轮与磁悬浮轴承的组合方案。某型号设备实测数据显示,与传统钢制飞轮相比,碳纤维复合飞轮减重达43%,转动惯量降低37%。这种轻量化设计直接减少了启动阶段的能量消耗,在连续8小时作业测试中,仅启动环节就节约电能19.6%。
动态平衡算法的升级是节能的核心突破。第三代自适应平衡系统通过256个采样点/秒的实时监测,将平衡调节响应时间缩短至0.8毫秒。某汽车零部件生产线的对比测试表明,该技术使平衡过程缩短40%,单次平衡作业能耗从3.2kW·h降至1.9kW·h。更精准的配重调节还减少了材料损耗,测试中配重块使用量下降28%。
在传动系统方面,永磁同步电机的应用带来显著效益。实测数据显示,在1500rpm工况下,新型电机效率达到96%,较传统异步电机提升11个百分点。配合变频驱动技术,设备在空载运行时功耗可自动降至额定功率的15%,这项改进使待机能耗下降62%。某轴承制造商年度用电报告显示,更换20台平衡机后,年节电量达38万度。
热管理系统的优化同样功不可没。采用相变材料与液冷循环的复合散热方案,使设备持续工作时的温升控制在8℃以内。温度稳定性提升带来两个直接效益:一是润滑系统工作负荷降低,油泵功耗减少23%;二是电子元件寿命延长,设备故障率下降45%,间接降低了维护过程中的能源消耗。
从实际应用案例来看,某大型电机生产企业对产线进行改造后,飞轮平衡工序的万元产值能耗从4.7度降至2.9度。按年产值3亿元计算,年节约用电54万度,相当于减少二氧化碳排放428吨。更值得注意的是,由于平衡精度的提升,产品不良率从1.2%降至0.6%,质量改进带来的节能效益甚至超过直接能耗节约。
智能控制系统的介入使节能效果再上新台阶。通过物联网平台收集的12个月运行数据表明,基于深度学习算法的预测性维护策略,可将设备能效波动范围控制在±3%以内。某航空部件工厂的应用案例显示,系统自动优化作业时序后,避开用电高峰期的策略使综合用电成本降低18%。
这些技术创新共同构成了飞轮平衡机的节能矩阵。实测数据证实,现代平衡机的单位产能能耗已较十年前下降52%,投资回收期缩短至14个月。随着《GB 30253-2013》能效标准的全面实施,新一代平衡机正在帮助制造业向绿色生产转型,其节能效益已从单一设备扩展到整个生产系统。
需要特别指出的是,不同行业应用存在差异化节能表现。在风电叶片平衡领域,由于工件尺寸特殊,节能效果可达58%;而在小型精密零件领域,节能率约为32%。这提示企业在设备选型时,需要结合具体工艺特点进行能效评估,才能最大化节能效益。