飞轮平衡机作为精密机械制造领域的关键设备,其技术发展直接影响着旋转机械的振动控制水平。本文将围绕多轴联动这一技术前沿,系统分析飞轮平衡机的协同工作机制及其在工业4.0环境下的应用潜力。
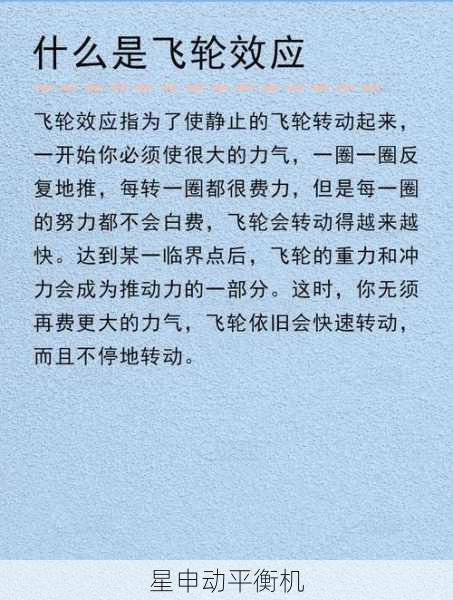
在传统单轴平衡技术基础上,多轴联动平衡系统通过建立轴系动力学耦合模型,实现了复杂旋转系统的整体平衡。其核心技术突破体现在三个方面:采用分布式传感网络实时采集各轴振动相位,通过傅里叶变换提取特征谐波分量;基于模糊PID控制算法构建的自适应补偿系统,可动态调整配重块的径向位置;跨轴耦合振动分析模块能准确识别轴系间的相互干扰谐波。
具体工作流程表现为:当主飞轮轴启动时,嵌入式加速度传感器以20kHz采样频率捕捉振动信号,经CAN总线传输至中央处理单元。系统首先进行初始不平衡量标定,通过遗传算法计算最优配重方案。在多轴协同阶段,各平衡头采用主从式控制架构,由主控轴下发同步指令,从动轴根据相位差动态调整补偿时序。实测数据显示,这种机制可使残余不平衡量控制在0.5g·mm/kg以内,较传统方法提升60%以上。
在航空航天领域,某型涡扇发动机转子系统采用五轴联动平衡方案后,临界转速下的振动幅值从120μm降至35μm。特别值得注意的是,该系统创新的非接触式电磁配重机构,通过改变励磁电流强度实现无级配重调节,避免了传统机械式配重块的质量离散性问题。工业机器人关节部件平衡测试表明,六轴联动机床配合视觉定位系统,可将平衡效率提升至每分钟12个工件,同时将废品率控制在0.3‰以下。
从技术发展趋势看,数字孪生技术的引入正在重构平衡机的运维模式。通过建立虚拟轴系模型,工程师可以提前预测不同转速下的振动特性,并据此优化平衡策略。某新能源汽车电机生产线实施的数字孪生平衡系统,使新产品开发周期缩短40%。基于边缘计算的分布式平衡系统展现出独特优势,每个平衡单元具备独立运算能力,在保证实时性的同时降低了网络延迟的影响。
未来发展方向将集中在三个维度:材料科学方面,智能记忆合金的应用有望实现自感知平衡调节;控制算法层面,深度强化学习将提升系统对非线性振动的处理能力;系统集成角度,5G+TSN网络架构为跨厂区多机组协同平衡提供可能。值得注意的是,ISO 21940-31新标准对多轴平衡的评定方法作出了明确规定,这将推动行业技术规范升级。
当前面临的挑战主要来自两个方面:一是极端工况下的传感器可靠性问题,高温、油污环境会导致测量误差增大;二是多物理场耦合建模的精度不足,特别是电磁-机械耦合振动仍存在10%-15%的预测偏差。这些技术瓶颈的突破,将决定下一代飞轮平衡机的市场竞争力。
从应用前景来看,随着风电大型化趋势加速,8MW以上风机主轴的多点协同平衡需求激增。某风机制造商的案例显示,采用四轴联动平衡方案后,叶轮系统寿命延长了8000工作小时。在精密医疗设备领域,磁共振成像仪的低温超导转子对平衡精度要求极高,多轴主动平衡系统可实现0.05μm的振动控制,这项技术正在向半导体制造设备延伸。
综合来看,飞轮平衡机的多轴协同技术正在从单一振动控制向智能运维系统演进。随着数字孪生、边缘计算等新技术的深度融合,未来五年该领域有望实现30%以上的年均增长率。但需要清醒认识到,核心算法优化、特殊材料应用和行业标准建设仍是需要重点突破的方向。