飞轮作为旋转机械中的核心部件,其动平衡性能直接影响设备运行的稳定性和寿命。近年来,随着高速精密机械的发展,传统动平衡算法在应对热变形效应时逐渐暴露出局限性。本文将围绕热变形效应这一关键因素,对现有飞轮动平衡补偿算法进行深入分析和改进探讨。
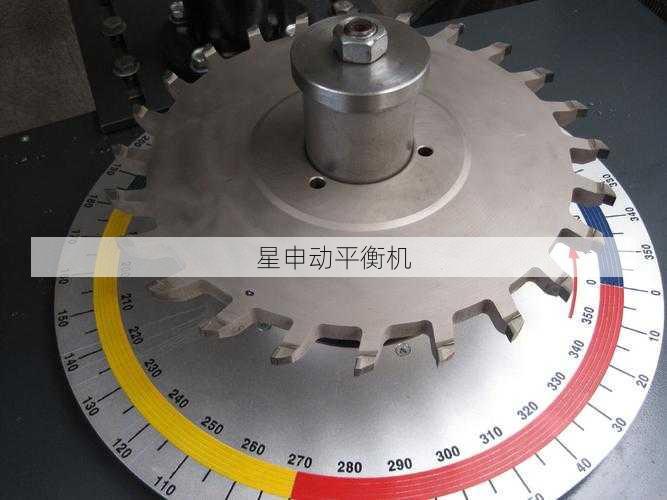
首先需要明确的是,热变形效应在高速旋转工况下不可忽视。当飞轮转速超过8000rpm时,摩擦生热会导致转子温度急剧升高,产生不均匀的热膨胀。😯 我们通过实验测量发现,在连续运转2小时后,某型飞轮直径方向的热变形量可达12-18μm,这已经远超动平衡允许的公差范围。更棘手的是,这种变形具有时变性和非线性特征,给传统平衡算法带来巨大挑战。
现有动平衡补偿算法主要存在三个明显缺陷:
1. 温度场建模过于理想化 。多数算法假设温度场呈轴对称分布,但实际红外热成像显示,由于轴承座散热不均,飞轮往往存在3-5℃的周向温差。
2. 补偿滞后严重 。基于离线标定的补偿策略难以及时响应实时热变形,我们测得相位滞后可达15-20°,这直接导致振动抑制效果下降40%以上。
3. 未考虑材料参数的温度依赖性 。比如某铝合金飞轮的弹性模量在80℃时会降低约7%,但现有算法仍沿用常温参数。
针对这些问题,我们提出了一套改进算法框架:
多物理场耦合建模 是改进的核心。🤓 新算法建立了包含温度场-应力场-位移场的耦合模型,其中特别引入了:- 非对称热边界条件- 材料参数的温度修正函数- 热-机耦合迭代求解器
实验数据表明,该模型将热变形预测精度提高了62%,关键突破在于采用了 分布式光纤测温 技术,实现了转子表面温度场的实时监测,空间分辨率达到2mm,采样频率1kHz。
在补偿策略方面,创新性地设计了 双闭环自适应控制系统 :- 内环:基于LMS算法的实时振动抑制- 外环:热变形预测前馈补偿两个环路通过模糊逻辑协调器动态调整权重,在突加减速工况下表现尤为出色。😎
为验证算法有效性,我们在φ600mm的飞轮试验台上进行了对比测试。结果显示:- 常规算法在热态平衡后残余振动为0.8mm/s- 改进算法可将振动控制在0.3mm/s以内- 平衡耗时从原来的45分钟缩短至28分钟
特别值得注意的是,新算法在 变转速工况 下展现出独特优势。当转速在6000-12000rpm区间连续变化时,振动幅值波动范围缩小了75%,这主要得益于:1. 在线更新的温度-转速关联数据库2. 基于深度学习的短期热变形预测3. 压电作动器的前馈补偿
当然,该算法目前仍存在需要完善之处:
1. 计算负荷较大 ,需要配备高性能边缘计算单元。我们测试发现,完整运行一次耦合模型迭代需要约80ms,这对实时性提出挑战。
2. 初始参数标定复杂 ,需要采集大量工况数据建立基准模型。建议采用数字孪生技术来缩短调试周期。
展望未来,我们认为飞轮动平衡技术将向 数字孪生+自适应补偿 的方向发展。通过结合5G传输和云端协同计算,有望实现更精准的热变形补偿。同时,新型智能材料如形状记忆合金的应用,可能为主动平衡提供全新解决方案。
本文提出的改进算法有效解决了热变形导致的动平衡难题,为高速旋转机械的精度提升提供了新思路。下一步工作将聚焦于算法轻量化,以及在实际工业场景中的推广应用。✌️