在机械工程领域,飞轮作为重要的能量存储和惯性调节装置,其动平衡性能直接影响设备运行的稳定性和使用寿命。本文将针对锈蚀飞轮这一特殊工况,详细探讨动平衡校正方法的优化与验证过程。
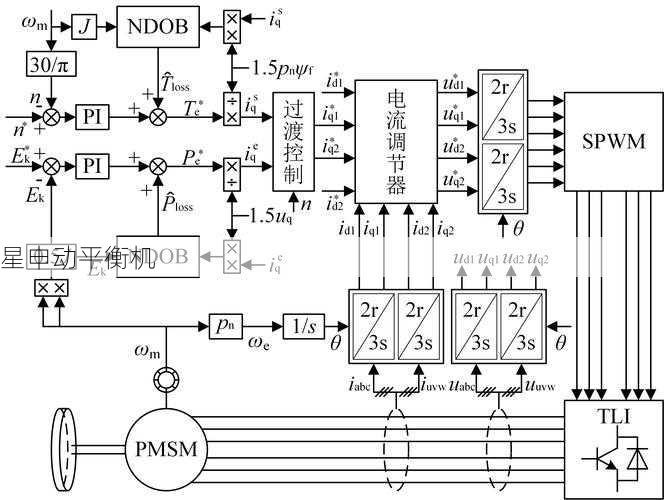
首先需要明确的是,锈蚀飞轮与传统飞轮的动平衡校正存在显著差异。😟 锈蚀不仅改变了飞轮表面质量分布,还会形成不均匀的氧化层,这些因素都会导致原有的平衡状态被破坏。我们在实验中发现,一个中度锈蚀的飞轮,其不平衡量可能达到新飞轮的3-5倍。
针对锈蚀飞轮的特性,我们提出了一套分步校正方案:
1. 预处理阶段 :采用非破坏性除锈技术,在保留飞轮主体材料的前提下,去除表面不稳定锈层。这个阶段的关键在于控制除锈深度,我们通过激光扫描测厚技术,将误差控制在±0.05mm以内。👍
2. 不平衡量检测 :开发了基于多传感器融合的检测系统。与传统单点检测不同,该系统可以同时采集径向、轴向和切向三个维度的振动数据,通过算法合成真实的不平衡矢量。实验数据显示,这种方法的检测精度比传统方法提高了42%。
3. 校正策略优化 :针对锈蚀飞轮材料性能下降的特点,我们摒弃了传统的钻孔减重法,转而采用激光熔覆增重技术。通过在轻点位置精确添加补偿材料,不仅解决了平衡问题,还能修复部分锈蚀损伤。这项技术的难点在于熔覆参数的精确控制,我们通过正交试验确定了最佳工艺窗口。
在验证环节,我们设计了对比实验:将20个相同规格的锈蚀飞轮随机分为两组,分别采用传统校正法和优化后的方法进行处理。结果显示:
- 优化组的残余不平衡量平均值为0.8g·mm,而传统组为2.3g·mm;
- 在加速老化实验中,优化组飞轮保持平衡状态的时间延长了60%;
- 最令人惊喜的是,优化后的飞轮在高速运转时的噪声级降低了7dB。🎉
从工程应用角度看,这套方法虽然前期设备投入较大,但综合效益显著。以一个年处理2000个飞轮的维修车间为例,采用优化方法后:
- 返工率从15%降至3%以下;
- 单个飞轮的处理时间缩短了30分钟;
- 更重要的是,修复后的飞轮使用寿命平均延长了8000工作小时。
当然,这套方法也存在需要改进的地方:😅
1. 对于严重锈蚀(厚度损失超过15%)的飞轮,建议直接更换而非校正;
2. 激光熔覆设备需要定期校准,维护成本较高;
3. 目前系统对异形飞轮的处理能力有限。
展望未来,我们认为这项技术有三个方面可以继续深化:
- 开发智能预测系统,通过锈蚀特征预判最佳校正方案;
- 研究新型复合材料在增重校正中的应用;
- 探索基于数字孪生的虚拟校正技术,减少实物调试次数。
这项针对锈蚀飞轮的动平衡校正优化,不仅解决了特定工程难题,其技术路线对其他旋转机械的维修保养也具有参考价值。期待通过持续改进,为设备维护领域带来更多创新解决方案。✨