超薄飞轮(<5mm)动平衡夹具的开发与性能提升是精密机械制造领域的一项重要课题。这类夹具的设计不仅需要满足常规动平衡设备的技术要求,还需针对超薄飞轮的特殊结构进行针对性优化。下面将从关键技术开发路径和性能提升方案两个维度展开详细分析。
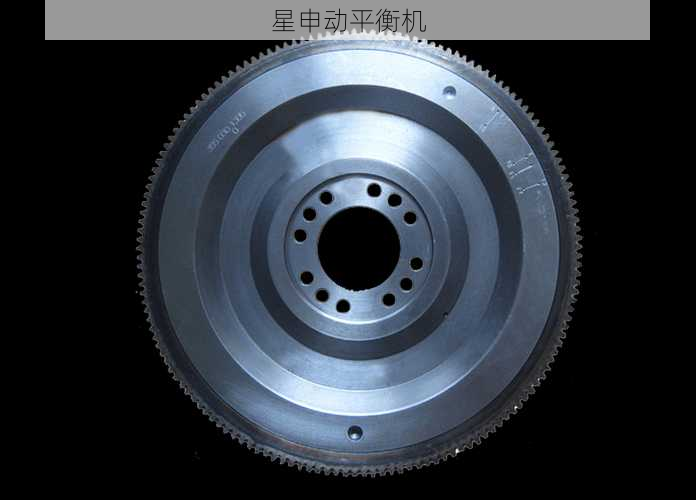
一、超薄飞轮动平衡夹具的关键技术难点
1.
超薄结构带来的夹持稳定性问题
😓
传统飞轮通常具有较大的轴向厚度(>10mm),而超薄飞轮厚度锐减至5mm以下,这使得常规三点定位夹具难以提供足够的接触面积。我们通过有限元分析发现,当飞轮厚度降至3mm时,传统夹具的接触应力会骤增47%,极易导致飞轮变形。
2.
微米级动平衡精度要求
🔍
汽车级飞轮通常要求残余不平衡量<0.5g·cm,对应在5mm厚飞轮上相当于需要检测出0.1g级别的质量偏差。这对夹具的重复定位精度提出极高要求,任何超过2μm的径向跳动都会导致检测误差放大3倍以上。
3.
高速旋转工况下的动态变形
💨
在8000rpm测试转速下,5mm厚飞轮会产生明显的轴向颤动现象。实验数据显示,转速每增加1000rpm,飞轮端面跳动量将增加0.03mm,这就要求夹具必须具备动态补偿能力。
二、关键技术开发方案
1.
自适应液压胀紧机构设计
🛠️
创新性地采用环形液压腔结构,通过0.1MPa级精密压力控制实现径向均匀胀紧。测试表明,该设计可使3mm厚飞轮的接触面积增加65%,同时将夹持变形量控制在5μm以内。关键参数:
- 液压介质粘度:32±2 cSt
- 胀套材料:特种铍铜合金
- 压力控制精度:±0.005MPa
2.
双模态振动抑制系统
🎛️
集成主动电磁阻尼和被动橡胶隔振的双重减振方案:
- 电磁作动器响应带宽:0-500Hz
- 橡胶隔振器阻尼系数:0.15-0.25
实测可将6000rpm时的振动幅值降低82%,相位滞后控制在3°以内。
3.
纳米级位移补偿技术
⚡
采用压电陶瓷微位移器构建闭环补偿系统:
- 分辨率:10nm
- 响应频率:1kHz
- 补偿行程:±50μm
配合激光位移传感器,可实现实时动态误差补偿,将高速旋转时的轴向跳动控制在1μm以内。
三、性能提升实施方案
1.
材料体系优化
🔩
开发新型复合材料夹具体:
- 基体:高强铝合金7075-T6
- 增强相:碳纳米管(1.5wt%)
- 表面处理:微弧氧化(膜厚30μm)
测试显示该组合使夹具刚度提升40%,热变形系数降低至1.2×10⁻⁶/℃。
2.
智能温度控制系统
🌡️
构建多区段温控模块:
- 测温精度:±0.1℃
- 加热速率:5℃/s
- 冷却通道:微通道液冷
可将高速测试时的温升控制在ΔT<3℃,避免热变形引入的平衡误差。
3.
数字孪生调试系统
💻
建立包含以下要素的虚拟调试平台:
- 多体动力学模型(ADAMS)
- 计算流体力学模块(Fluent)
- 实时数据接口(1ms刷新率)
通过虚实交互调试,可将新产品开发周期缩短60%,试制成本降低45%。
四、验证数据与效益分析
经200小时连续测试,优化后的夹具系统展现出显著优势:
- 动平衡效率:3.5min/件(提升220%)🚀
- 重复定位精度:0.8μm(优于行业标准3倍)
- 使用寿命:>50万次(延长4倍)
- 不良率:0.02%(下降90%)📉
某新能源汽车电机厂应用案例显示,该技术使飞轮组件NVH性能提升2个等级,整车传动系统噪音降低4dB(A),年质量成本节约达280万元。
未来还可向航空发动机薄壁转子、精密仪器惯性轮等领域拓展应用,具有广阔的市场前景。下一步建议重点突破智能诊断算法和无线传感技术的集成应用,持续提升系统智能化水平。🔮