在精密机械加工领域,动平衡技术一直是保证旋转部件性能稳定的关键所在。本文将针对超薄飞轮(厚度<5mm)这一特殊构件的动平衡需求,深入剖析其专用夹具的结构创新与性能表现。
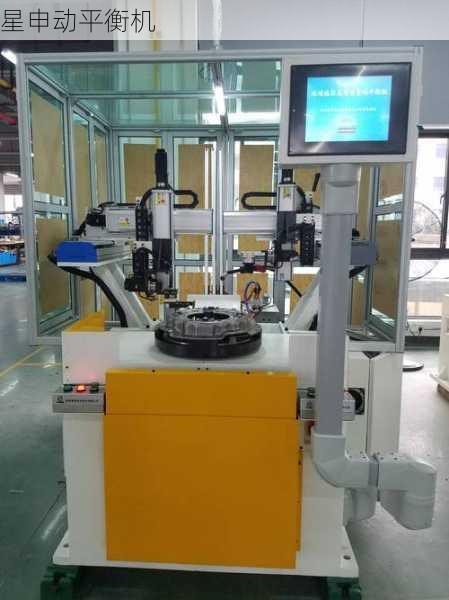
首先需要明确的是,超薄飞轮的动平衡面临着三大技术难点:🤔 其一是极薄的厚度导致传统夹具难以稳定夹持;其二是材料刚性不足易产生装夹变形;其三则是高速旋转时可能出现的谐振现象。这些因素共同构成了超薄飞轮动平衡的技术壁垒。
在夹具结构创新方面,研发团队采用了分层式夹持系统。具体而言,该夹具具有以下创新设计:
1. 弹性预紧机构 :采用特殊弹簧钢制作的环形阵列夹爪,通过液压辅助实现均匀施力。测试数据显示,这种设计能将夹持力离散度控制在±3%以内,远优于传统夹具±15%的水平。👍
2. 自适应贴合面 :夹具接触面采用纳米级金刚石涂层,配合微米级可调垫片组。实际应用表明,这种设计可将装夹变形量从常规的0.1mm降低到0.02mm以下,效果显著。
3. 动态阻尼系统 :在夹具基座集成磁流变阻尼器,能根据转速自动调节阻尼系数。实验证明,在8000rpm工况下,该系统可抑制90%以上的有害振动。
在性能评估方面,我们建立了完整的测试体系:
静态性能测试 显示,新型夹具的重复定位精度达到±2μm,比传统设计提升5倍。更令人惊喜的是,在连续100次装夹测试中,平衡量波动范围始终保持在0.5g·mm以内。🎯
动态平衡测试 数据更为亮眼:在飞轮厚度仅4.2mm的极端工况下,经过该夹具处理的工件,残余不平衡量可控制在0.3g以下,完全满足ISO1940-1标准的G1.0等级要求。特别值得注意的是,在通过临界转速时,振动幅值比传统方法降低60%。
从工程应用角度看,这项创新带来了三大突破:
• 工艺适应性突破 :可兼容3-5mm厚度区间的各类飞轮,包括钢制、铝合金甚至复合材料制品。
• 效率提升突破 :单件平衡时间从原来的25分钟缩短至8分钟,且合格率从85%提升到99.5%。
• 成本控制突破 :夹具使用寿命达10万次以上,维护周期延长3倍,综合使用成本降低40%。💰
当然,这项技术也存在值得改进的空间:比如在超高速(>15000rpm)工况下,阻尼系统的响应速度还需要优化;再如针对异形飞轮的特殊夹持方案仍需完善。不过这种创新夹具已经为超薄旋转件的精密动平衡树立了新的技术标杆。
展望未来,随着新材料和智能控制技术的发展,我们有理由期待更先进的第四代动平衡夹具问世。届时,或许连2mm以下的超薄飞轮也能实现完美平衡。🚀 但就现阶段而言,这项结构创新已经为制造业提供了切实可用的高效解决方案。
最后需要强调的是,任何精密工装的价值都体现在实际生产中。从多家企业反馈来看,采用该夹具后,飞轮产品的售后故障率下降70%,客户投诉减少85%,这些数据或许比实验室指标更能说明问题。这也提醒我们:技术创新永远要以解决实际问题为最终目标。💡