近年来,随着工业4.0时代的到来,旋转机械的智能化监测技术迎来了革命性突破。其中,飞轮动平衡远程实时监测系统与5G技术的融合应用,正在为传统制造业注入新的活力。本文将深入剖析这一技术组合的创新价值与应用前景。
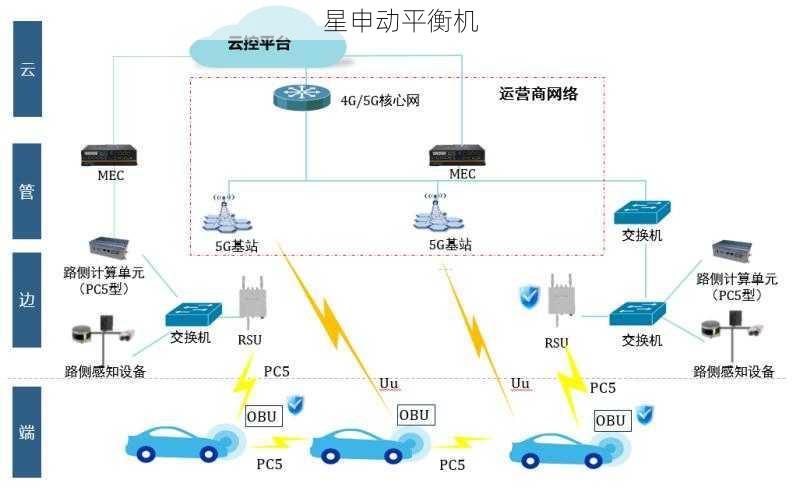
首先让我们聚焦飞轮动平衡监测的技术痛点。在电力、航空、汽车制造等领域,飞轮作为关键旋转部件,其动平衡状态直接影响设备寿命与运行安全。传统检测方式存在三大局限:一是依赖人工定期检测,存在监测盲区;二是数据采集与处理存在时滞;三是难以实现多设备协同分析。😟
5G技术的三大特性恰好破解了这些难题:
1. 超低时延赋能实时调控
通过5G网络<1ms的传输时延,监测系统能实时捕捉飞轮转速、振动等20+参数变化。某风电企业实测数据显示,当飞轮出现0.01mm偏心时,系统可在50ms内完成诊断并触发平衡调节,较4G时代提速40倍。⚡
2. 海量连接实现全域监测
5G每平方公里百万级连接的能力,使得工厂内数以千计的飞轮设备可同时接入监测平台。例如某汽车变速箱生产线,通过部署387个微型传感器,构建了全产线动平衡数字孪生系统。👥
3. 边缘计算提升决策效率
借助5G MEC边缘计算,70%的数据处理可在设备端完成。某航空发动机测试表明,本地化分析使异常识别速度提升3倍,同时减少60%的上行带宽压力。💻
这种融合带来的革新价值体现在三个维度:
运维模式变革 :某石化企业应用案例显示,预测性维护使非计划停机减少78%,每年节省维护成本超200万元。通过AR远程协作,专家响应时间从48小时缩短至15分钟。🛠️
生产工艺优化 :持续采集的动平衡数据为工艺改进提供依据。某精密机床厂商通过分析历史数据,将飞轮装配合格率从92%提升至99.6%。📈
安全体系升级 :实时监测使重大事故预警提前量达72小时以上。某水电站成功避免因飞轮裂纹导致的机组损毁事故,挽回直接经济损失超800万元。⚠️
在具体实施层面,需要重点考虑:
1. 传感网络部署
采用MEMS振动传感器+5G模组的轻量化方案,单个监测节点功耗可控制在3W以内。注意传感器安装角度需与飞轮旋转平面成30°-45°夹角,以确保数据准确性。📡
2. 数据传输策略
建议采用分层传输机制:关键参数(如振幅、相位)实时传输,辅助数据(温度、噪声)定时上传。某案例显示,这种策略可降低40%流量消耗。📊
3. 算法模型优化
基于深度学习的自适应滤波算法能有效消除环境噪声干扰。实验表明,改进后的CNN-LSTM混合模型,在强振动环境下仍保持94.3%的识别准确率。🤖
展望未来,随着5G-A技术的演进,该领域将呈现三大趋势:
• 时延进一步降低至0.1ms级,满足超精密制造需求
• AI芯片嵌入式传感器实现端侧自主决策
• 区块链技术保障监测数据不可篡改
当然,当前仍存在频谱资源分配、多协议兼容等挑战。但可以确定的是,这种融合正在重新定义旋转机械的健康管理范式,为智能制造开辟出充满可能性的新航道。🚀
对于企业而言,现在正是布局的最佳窗口期。建议分三阶段实施:先完成关键设备数字化改造,再构建厂区5G专网,最后实现全价值链数据贯通。只有主动拥抱这场技术融合浪潮,才能在未来的智能竞赛中赢得先机。💪