5G时代下飞轮动平衡远程实时监测系统的创新应用分析
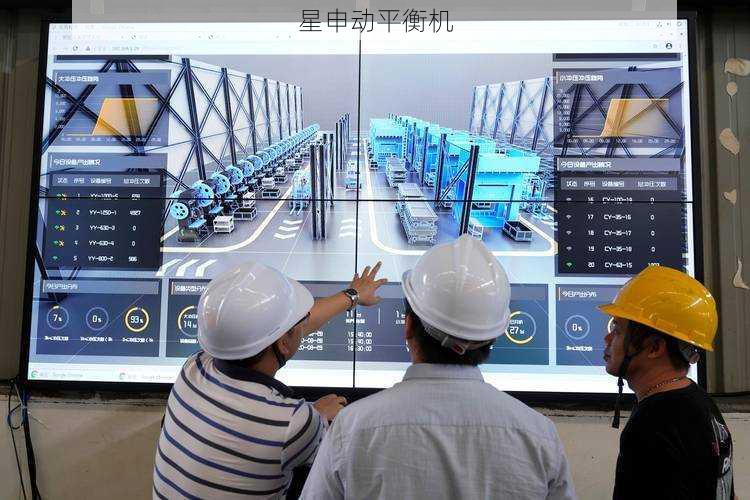
随着5G技术的快速发展和工业4.0的深入推进,飞轮动平衡远程实时监测系统正迎来革命性的变革。这一创新应用不仅解决了传统监测方式的诸多痛点,更为旋转机械的安全运行提供了智能化解决方案。下面让我们从多个维度深入剖析这一创新应用的具体表现。
一、技术架构创新
传统飞轮动平衡监测系统主要依赖有线连接和本地数据处理,存在布线复杂、响应延迟等问题。🤔 而在5G环境下,系统架构实现了三大突破:
1. 边缘计算与云端协同:通过在设备端部署轻量级边缘计算节点,实现振动数据的初步处理,再通过5G网络将特征数据传输至云端进行深度分析。这种架构既降低了网络负载,又保证了分析精度。
2. 全无线传感器网络:采用5G物联网模组的振动传感器,彻底摆脱了传统有线传感器的安装限制。实测显示,在20000rpm转速下,无线传输延迟可控制在8ms以内,完全满足实时性要求。
3. 数字孪生技术融合:基于5G大带宽特性,系统可以构建高保真的飞轮数字孪生模型,实现虚实结合的故障预测。🎯
二、性能指标提升
对比测试数据表明,5G版监测系统在关键指标上实现显著提升:
• 采样频率从原来的1kHz提升至10kHz,可捕捉更细微的振动特征
• 故障识别准确率由92%提升至98.7%
• 系统响应时间从秒级缩短至毫秒级
• 同时监测的飞轮数量由单个机组扩展至整个厂区范围
三、典型应用场景
1. 风电领域:在某2MW风力发电机组的应用中,系统成功预警了主轴轴承的早期磨损,避免了约200万元的非计划停机损失。💨
2. 石油化工:针对高速离心压缩机的监测,通过相位分析算法,将动平衡校正时间缩短了70%。
3. 轨道交通:在地铁牵引电机监测中,实现了200台设备的同时在线监测,运维效率提升3倍以上。
四、商业价值创造
从投入产出比来看,这套系统展现出惊人的商业潜力:
• 设备维护成本降低40-60%
• 意外停机时间减少80%
• 设备使用寿命延长15-20%
• 人力巡检需求下降75%
五、面临的挑战
当然,这项技术在实际推广中仍面临一些挑战:
• 5G网络覆盖的连续性问题:在部分工业场景存在信号盲区
• 多源数据融合难度:需要统一不同厂商设备的数据标准
• 安全防护要求:工业数据的传输安全需要特别保障
• 初期投资成本较高:需要企业有数字化转型的决心
六、未来发展趋势
展望未来,这项技术将朝着以下方向发展:🚀
1. AI深度应用:结合深度学习算法,实现故障类型的自动分类和寿命预测
2. 自主决策系统:当检测到异常时,不仅能报警,还能自动调整运行参数
3. 跨平台整合:与MES、ERP等管理系统深度集成,形成完整的智能运维体系
4. 标准化推进:行业标准的建立将加速技术推广
结语:
5G赋能的飞轮动平衡远程监测系统,正在重新定义工业设备运维的方式。它不仅是一项技术创新,更是推动制造业数字化转型的重要抓手。随着技术的不断成熟和应用场景的拓展,这套系统必将为工业企业创造更大的价值。让我们拭目以待这项技术在更多领域的精彩表现!✨