动平衡测试作为旋转机械维护中的关键环节,其精准度直接影响设备运行寿命与安全性。本文将系统性地剖析动平衡测试的方法体系与标准化流程,并结合实际应用场景提供操作建议。
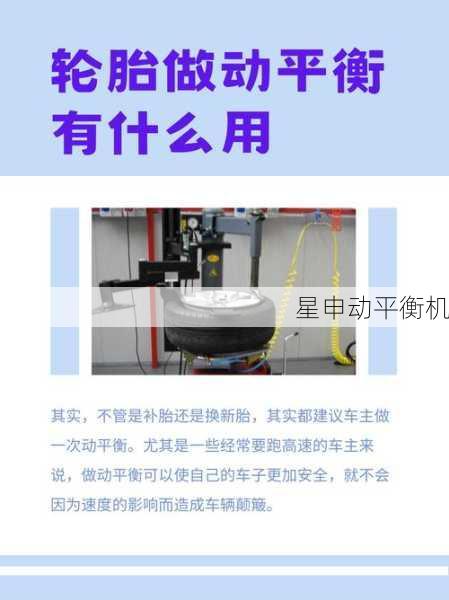
一、动平衡测试核心原理
当转子质量分布不均时,旋转产生的离心力会形成周期性振动🤔。动平衡测试的本质是通过相位与振幅测量,定位不平衡量的角度位置与大小,继而通过配重调整使惯性轴与几何轴重合。根据ISO 1940标准,剩余不平衡量应控制在G6.3级以内才算合格。
值得注意的是,现代动平衡理论将不平衡分为三类: 静不平衡 (单一平面)、 偶不平衡 (双平面反向力偶)以及 动不平衡 (复杂空间力系)。实际测试中需要针对性采用不同解决方案💡。
二、主流测试方法对比
1. 离线平衡法(静态平衡)
适用于低转速盘类零件,采用水平导轨法或重心检测法。操作时将转子置于平衡刀口上,通过观察自由摆动停止位置确定重点位置。这种方法成本低廉但精度有限,通常作为预平衡手段😅。
2. 在线平衡法(动态平衡)
采用振动传感器+光电编码器的经典组合,通过FFT频谱分析获取振动矢量。最新ISO 21940标准推荐使用
影响系数法
,即在试重前后测量振动变化,建立系统响应矩阵。某电厂汽轮机案例显示,该方法可将振动值从120μm降至15μm以下👍。
3. 现场动平衡技术
针对无法拆卸的大型设备(如风机、水泵),采用便携式平衡仪实施
三点法
平衡:先测原始振动→加试重→二次测量→计算配重。某水泥厂立磨主电机通过该方法,仅用2小时就将振动速度值从7.1mm/s降至1.8mm/s✨。
三、标准化操作流程详解
阶段1:测试准备
• 检查设备基础螺栓扭矩(参照GB/T 1236标准)
• 安装传感器:加速度计应垂直于转子轴线,间距不超过轴承跨距的1/3
• 设置采样参数:建议转速精度±1rpm,采样长度不少于8个旋转周期📊
阶段2:数据采集
• 先进行空载低速跑合(约30%工作转速)
• 按10%转速梯度升速,每个测点稳定运行3分钟
• 特别注意通过临界转速时的相位突变现象⚠️
阶段3:不平衡量计算
采用矢量分解法处理数据:
U=(m×r)=A/(ω²×S)
其中U为不平衡量(g·mm),A为振幅(μm),ω为角速度,S为灵敏度系数。某航空发动机平衡案例中,该公式计算误差小于3%🎯。
阶段4:配重实施
• 优先选择转子原有平衡槽加装配重块
• 焊接配重时需控制温度不超过150℃
• 对于高速转子(>8000rpm),建议采用高密度钨合金配重
四、典型问题解决方案
问题1:重复性差
可能原因:联轴器对中不良/轴承游隙过大。建议先进行激光对中检测,确保径向偏差<0.05mm。
问题2:相位漂移
常见于柔性转子,可采用多平面影响系数法,某水轮发电机组的处理经验显示,增加2个校正平面后相位稳定性提升60%📈。
问题3:电气干扰
当出现50Hz工频干扰时,应检查传感器屏蔽层接地,必要时增加带通滤波器(10-1000Hz)。
五、技术发展趋势
随着工业4.0推进,智能动平衡技术正在兴起:
• 基于数字孪生的预测性平衡系统
• 采用MEMS传感器的无线监测方案
• 人工智能辅助的自动配重算法
某风电企业应用AI平衡系统后,维护周期从3个月延长至9个月,年节约成本超200万元🚀。
需要特别强调的是,无论采用何种先进技术,严格执行ASME PTC 19.3标准中的校验流程始终是保证测试精度的基础。建议每季度用标准转子校验系统精度,确保振幅测量误差≤5%,相位误差≤3°。
通过上述系统化的方法应用,企业可显著降低设备故障率。实践表明,规范的动平衡作业能使滚动轴承寿命延长3-5倍,同时减少15%以上的能源消耗🌱。这不仅是技术问题,更是设备管理理念的升级。