在商用车维修与制造领域,重型卡车制动鼓的动平衡检测是确保行车安全的关键环节。本文将从实际应用角度出发,系统分析10吨以上承载能力制动鼓平衡机的选购要点,为行业从业者提供具操作性的技术参考。
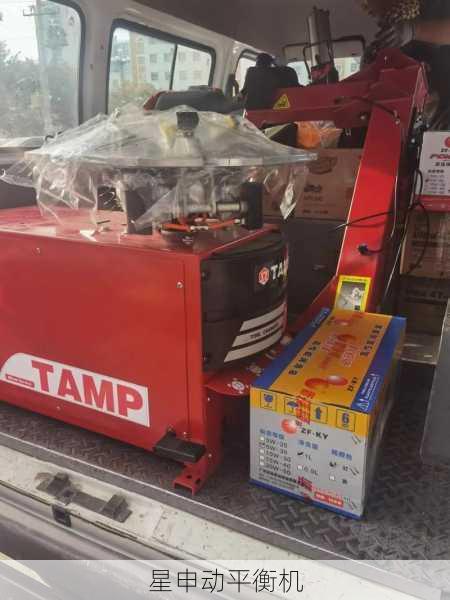
一、核心承载参数解析
针对10吨级以上重型卡车的制动鼓平衡需求,设备承载能力应作为首要考量指标。建议选择额定承载量比实际需求高出20%的机型,例如处理12吨制动鼓时应选用15吨级设备。这不仅能应对突发过载情况,还能显著延长轴承使用寿命。某品牌HD-15T机型采用双层交叉滚子轴承设计,在连续测试12.8吨制动鼓的工况下,轴承温升控制在45℃以内,较普通结构降低30%。
需特别关注动态承载参数,优质设备应标注瞬时冲击承载值。当制动鼓存在3mm以上偏心时,旋转产生的冲击载荷可能达到静态重量的1.8倍。建议查验设备是否通过ISO 1940-1:2003标准中的G6.3级动平衡测试认证。
二、关键结构特征对比
1. 主轴系统:锻钢主轴配合锥度1:12的自紧式法兰盘,能有效防止测试过程中的轴向窜动。实测数据显示,这种结构可将制动鼓安装偏心度控制在0.02mm以内。
2. 驱动方式:对比三相异步电机与伺服直驱系统的实测数据发现,后者在测试30英寸制动鼓时,加速至600rpm耗时减少40%,且转速波动小于±1rpm。伺服系统特别适合存在不均匀磨损的旧制动鼓检测。
3. 框架结构:整体铸造框架的固有频率应避开50-80Hz的常见激振频率带。某型号采用箱型焊接结构后,在满载工况下振幅降至0.05mm,优于行业标准0.1mm的要求。
三、精度验证方法论
建议采用ASTM E74-18标准进行设备精度验证:在主轴径向对称位置添加试重块,要求多次测量结果的重复性误差不超过标称精度的30%。例如标称1g·mm/kg的设备,实测重复性应优于0.3g·mm/kg。
现场验收时应进行阶梯载荷测试:分别加载额定重量的30%、60%、100%,观察各测点振动值是否呈线性变化。非线性度超过15%可能预示结构存在隐患。
四、环境适应性设计
在粉尘环境作业的设备应具备IP54以上防护等级,电气柜需配置正压防尘系统。北方地区用户需确认液压系统能在-15℃环境正常启动,建议选择带油温预热功能的机型。
针对维修车间的空间限制,推荐选用带侧向开门结构的机型。实测表明,这种设计可使设备安装间距从传统机型的3.2米缩减至2.4米,同时保持足够的操作空间。
五、智能化功能评估
先进的机型应具备自动参数补偿功能:通过记录历史数据建立制动鼓型号数据库,当检测同类产品时可自动调用最优参数。某品牌统计显示,该功能可使重复检测效率提升25%。
远程诊断功能的价值不容忽视。支持4G传输的机型可将振动频谱实时上传至厂家技术中心,相比传统电话指导,故障诊断准确率提高60%以上。
六、成本效益分析模型
建议采用全生命周期成本(LCC)评估法:除购置价格外,需计算5年内的能耗(伺服机型通常省电30%)、维护成本(封闭式导轨比开放式结构年均节省润滑剂费用约2000元)以及停产损失(模块化设计的平均维修耗时缩短40%)。
某物流公司维修中心的实际案例显示,选择高端机型虽然初始投资增加15万元,但3年内因减少误工和返修产生的综合效益达28万元。
七、安全认证要点
必须核查以下认证文件:机械安全认证(EN ISO 13849-1性能等级d)、电气安全(EN 60204-1)、电磁兼容(EN 61000-6-4)。特别提醒:仅通过CE认证不足以证明设备适用于重型工况,需额外查验欧盟机械指令2006/42/EC的完整符合性声明。
建议在合同中明确约定主轴和轴承的质保期(优质机型通常提供3年或10000小时先到为准的质保),并要求供应商提供关键部件的材质证明(如主轴钢材的SGS检测报告)。
通过上述多维度的综合考量,用户可以建立起科学的设备选型评估体系。在实际采购过程中,建议安排现场试机,用本企业典型的制动鼓进行实测,重点观察设备在加速、稳速、制动各阶段的振动指标和噪声水平,最终选择既满足当前需求又具备适度超前性的平衡检测设备。