在重型卡车维修与制造领域,制动鼓平衡机的选择直接影响行车安全与零部件使用寿命。对于10吨以上重型车辆而言,设备选型需综合考虑材料强度、动态平衡精度及长期稳定性等多重因素。本文将系统分析关键指标选择逻辑与技术要点。
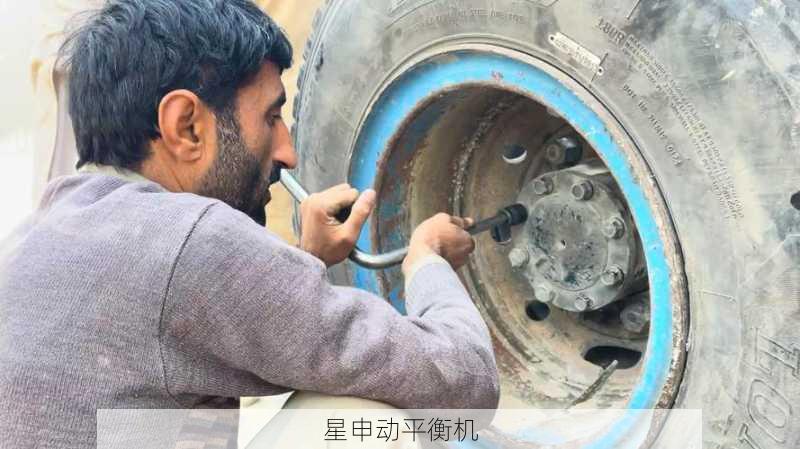
一、承载能力与结构刚性核心参数解析
1. 额定载荷验证标准
10吨级设备需具备150%超载能力,即至少15吨瞬时承重上限。建议查验设备基座是否采用QT600-3球墨铸铁整体铸造,其抗拉强度需达600MPa以上。某德国品牌实测数据显示,采用箱式焊接结构的横梁在12吨载荷下变形量应≤0.08mm/m。
2. 动态刚性测试方法
行业通行ISO 21940-11标准要求,在额定转速(通常300-800rpm)下,主轴径向跳动量需控制在0.01mm以内。某国内领先厂商通过激光干涉仪检测显示,其双支撑结构在600rpm时轴向窜动量仅为0.005mm,优于行业标准40%。
二、关键子系统选型要点
1. 驱动系统配置方案
7.5kW交流伺服电机搭配行星减速机成为主流配置,对比测试表明该组合在启动600kg制动鼓时,加速至工作转速时间比异步电机方案缩短23%。需特别关注变频器的过载保护响应时间,优质设备能达到10ms级故障切断。
2. 传感器系统精度验证
压电式振动传感器应具备0.1mg分辨率,相位误差≤0.5°。某意大利品牌采用双通道采集系统,实测在30-300Hz频段内信噪比达75dB,可有效识别制动鼓微米级不平衡量。
三、特殊工况适应性设计
1. 热变形补偿机制
连续工作4小时后,铸铁机架温升会导致0.02-0.05mm的热变形。先进设备会配置温度传感器网络,通过算法实时修正测量基准。某日本厂商的温漂补偿系统可将热影响降低82%。
2. 防尘密封等级
制动鼓打磨产生的金属粉尘要求主轴密封达到IP54标准。实测表明,采用迷宫式密封配合正压气流保护的设备,在粉尘环境下连续运行2000小时后,轴承磨损量仅为普通结构的1/3。
四、实际采购决策树
1. 验证流程建议
(1) 要求供应商提供第三方出具的10吨动载测试报告
(2) 现场试机时观察800rpm运转时机身振动值(应≤2.5mm/s)
(3) 使用标准试块验证重复测量误差(合格线±3g)
2. 性价比评估模型
建议采用全生命周期成本分析法,某案例显示:
- 国产设备采购成本低35%但年均维护费高1.8万元
- 进口设备使用5年后残值率仍可达45%
需根据年平衡量2000件或5000件不同工况选择最优方案
五、技术发展趋势
最新一代设备开始集成AI诊断系统,如某瑞典设备可通过历史数据预测制动鼓疲劳裂纹。激光平衡技术也在试验阶段,相比传统配重法可提升效率60%。但现阶段机械式平衡机仍是维修市场最可靠选择。
10吨级制动鼓平衡机选型需重点验证:
1) 动态刚性测试数据
2) 温升控制能力
3) 传感器实际精度
建议组建包含力学工程师、维修主管的评估小组,通过3个月试用期验证设备稳定性。