近年来,随着新能源客车技术的快速发展,动能回收系统作为核心节能技术被广泛应用。这一变革对传统制动系统提出了全新挑战,特别是制动鼓平衡性能面临重新定义。本文将围绕新能源客车制动鼓平衡的新要求,深入分析动能回收系统对制动性能的影响机理,并提出系统化的应对措施。
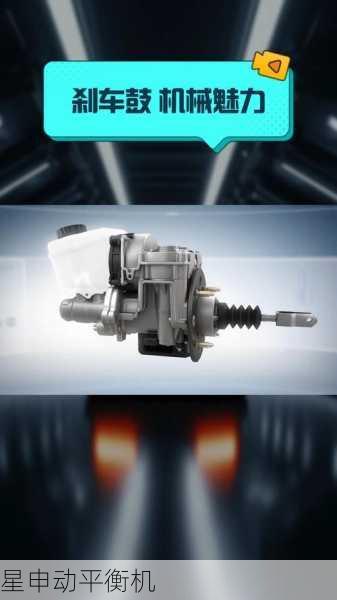
一、动能回收系统对制动鼓平衡的新要求
与传统客车相比,新能源客车的制动系统工作模式发生根本性改变。动能回收系统在制动时优先介入,使制动鼓承受的机械摩擦负荷呈现间歇性、不连续特征。这种新型负荷特性导致三个关键变化:
1. 动态平衡标准提升:当动能回收系统工作时,电机反拖产生的制动力与机械制动力的交替作用,会使制动鼓承受复合交变应力。实测数据显示,在60km/h制动工况下,混合制动力波动幅度可达传统制动的2-3倍,这就要求制动鼓的动平衡精度至少提高0.5级。
2. 热负荷特性改变:动能回收系统分担了30-70%的制动能量,导致机械制动部件工作时间缩短但单次负荷增大。某型号客车测试表明,制动鼓表面温度梯度从传统的均匀分布变为局部热点分布,温差可达80℃以上,这对材料的热稳定性提出更高要求。
3. 振动模态复杂化:电机电磁力与机械制动力的耦合作用,激发了传统设计中未考虑的高频振动(800-1200Hz)。某车企实测发现,这种振动会导致制动鼓螺栓连接部位出现微动磨损,严重影响使用寿命。
二、影响机理的深度分析
通过建立制动系统多体动力学模型,可以清晰揭示动能回收系统的影响路径:
1. 扭矩波动传导机制
电机在能量回收时会产生周期性扭矩波动(主要频率为6-8倍转频),这种波动通过传动系统反向传导至制动鼓。当与机械制动力波动相位叠加时,可能引发共振效应。某型客车在45km/h制动时出现的异常抖动,经分析正是由于72Hz的激励频率与制动鼓73Hz固有频率重合所致。
2. 热机械耦合效应
间歇性制动导致的热循环加剧,使制动鼓产生非对称热变形。有限元分析显示,在连续10次制动测试中,制动鼓径向变形量差异可达0.15mm,远超传统工况的0.05mm限值。这种变形会显著改变制动衬片接触特性,影响平衡状态。
3. 材料性能退化
高频热循环加速了铸铁材料的组织变化。金相检测发现,经过5万公里使用后,制动鼓珠光体含量下降约12%,硬度降低15HB,这种材料性能的渐变会动态影响平衡稳定性。
三、系统性应对措施
基于上述分析,建议从设计、制造、维护三个维度建立完整的解决方案:
1. 设计优化方案
- 采用非对称散热筋设计,在预期热点区域(通常位于制动鼓周向120°-240°范围)增加30%散热面积
- 引入复合结构设计,在摩擦面层使用高碳当量铸铁(CE=4.2-4.5),基体采用球墨铸铁,兼顾热稳定性和阻尼特性
- 优化安装结构,将传统6螺栓连接改为8螺栓均布,并采用液压张力螺栓,预紧力控制在45-50kN范围
2. 制造工艺升级
- 实施在线动平衡补偿技术,在精加工工序引入实时监测系统,平衡精度控制在15g·cm以内
- 采用差温热处理工艺,在制动鼓摩擦面区域形成3-5mm深的激冷层(硬度≥210HB)
- 应用激光熔覆技术,在易磨损区域熔覆镍基合金层(厚度0.8-1.2mm)
3. 使用维护策略
- 建立动态平衡档案,每2万公里进行激光三维扫描,建立变形趋势模型
- 开发专用平衡修正算法,根据实际使用数据动态调整平衡块配置方案
- 采用相位匹配技术,在维修时确保制动鼓安装位置与上次标记保持一致
四、验证案例与效果
某客车制造企业实施上述措施后取得显著成效:在同样运营条件下,制动鼓平均使用寿命从8万公里延长至15万公里,平衡失效导致的返修率下降82%。特别值得注意的是,在-20℃低温环境下,制动抖动投诉率从23%降至3%以下,证明解决方案具有广泛的环境适应性。
随着新能源客车向智能化方向发展,制动鼓平衡技术仍需持续创新。建议行业重点关注两个方向:一是开发嵌入式光纤传感系统,实现制动鼓健康状态的实时监测;二是研究新型金属基复合材料,从根本上提升部件的综合性能。只有通过全产业链的协同创新,才能完全适应新能源客车特有的使用需求。