近年来,随着新能源客车技术的快速发展,动能回收系统已成为提升能源利用效率的关键技术之一。这一技术的广泛应用也对传统制动系统提出了新的要求,尤其是在制动鼓平衡方面。本文将围绕新能源客车制动鼓平衡的新要求,分析动能回收系统下的测试标准与技术挑战。
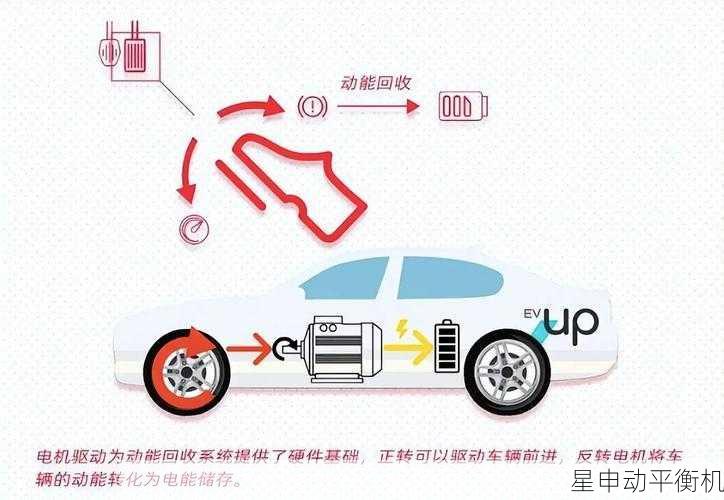
新能源客车与传统燃油客车在制动系统上存在显著差异。传统燃油客车主要依赖摩擦制动,而新能源客车则通过动能回收系统将制动能量转化为电能储存。这一变化使得制动鼓的工作环境更加复杂。在动能回收系统介入时,制动鼓的受力状态会发生动态变化,传统的平衡测试标准已无法完全适用。因此,制定新的测试标准成为行业亟需解决的问题。
新的测试标准需要综合考虑动能回收系统与摩擦制动的协同作用。例如,在制动过程中,动能回收系统的介入时机和力度会影响制动鼓的受力分布。测试标准应包含不同回收强度下的平衡性能评估,以确保制动鼓在多种工况下均能保持稳定。还需考虑频繁制动对制动鼓材料的疲劳影响,这对测试设备的精度和测试方法的科学性提出了更高要求。
技术挑战方面,动能回收系统的动态特性增加了制动鼓平衡控制的难度。传统平衡测试通常在静态或匀速条件下进行,而新能源客车的制动过程往往伴随剧烈的动态变化。如何在高动态条件下准确测量制动鼓的平衡状态,是技术研发的重点之一。目前,部分企业开始采用高精度传感器和实时数据处理技术,但如何将这些技术标准化并推广,仍需进一步探索。
材料科学也是制动鼓平衡技术的重要研究方向。动能回收系统的频繁使用会导致制动鼓温度变化更加剧烈,这对材料的耐热性和热稳定性提出了更高要求。新型复合材料或涂层技术的应用可能成为解决这一问题的关键。例如,某些陶瓷基复合材料在高温下仍能保持良好的机械性能,但其成本和生产工艺仍是推广的瓶颈。
从制造工艺角度看,制动鼓的加工精度直接影响其平衡性能。传统加工工艺可能难以满足新能源客车对制动鼓的高精度要求。数控加工技术和智能化检测设备的引入,有助于提升制动鼓的加工质量和一致性。这些先进设备的投入成本较高,对中小企业构成了一定挑战。
在标准制定层面,目前国内外尚未形成统一的新能源客车制动鼓平衡测试标准。各企业多采用自行制定的内部标准,这不利于行业整体技术水平的提升。建议相关行业协会牵头,联合整车厂、零部件供应商和科研机构,共同制定兼顾安全性和经济性的行业标准。标准应涵盖测试条件、评价指标、限值要求等关键内容,并考虑不同气候和路况的适应性。
未来发展趋势方面,随着车联网技术的普及,制动鼓平衡状态的实时监测可能成为标配功能。通过安装振动传感器和温度传感器,结合云端数据分析,可以提前发现平衡异常并预警。这种预测性维护模式将显著提升行车安全性,但需要解决数据采集的可靠性和传输稳定性等技术问题。
新能源客车制动鼓平衡面临的新要求主要源于动能回收系统的应用。解决这一问题需要从测试标准、材料科学、制造工艺等多个维度进行创新。行业应加快制定统一标准,推动高精度检测技术和新型材料的研发应用,同时探索智能化监测方案,以全面提升新能源客车制动系统的可靠性和安全性。
最后需要指出的是,制动鼓平衡技术的进步不仅关系到单车性能,还对整个新能源汽车行业的可持续发展具有重要意义。通过不断优化制动系统,可以进一步提高能源利用效率,延长零部件使用寿命,降低维护成本,从而增强新能源客车的市场竞争力。这需要产业链各环节的紧密协作和持续投入。