在现代工业生产中,飞轮作为重要的储能和稳定转速的机械部件,其动平衡性能直接影响设备运行的可靠性和使用寿命。特别是在复杂工况条件下,如变转速、变负载、高温等环境下,飞轮平衡机的精准控制与振动抑制显得尤为重要。本文将围绕这一主题,从技术原理、控制策略和振动抑制方法三个维度展开深入探讨。
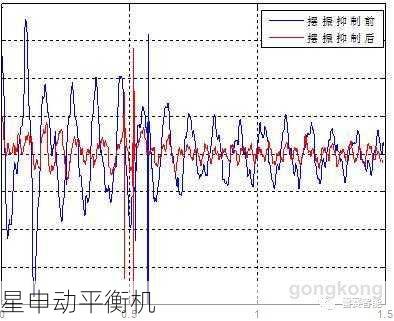
首先需要明确的是,飞轮不平衡产生的根本原因在于质量分布不均匀。当飞轮高速旋转时,这种不均匀性会产生周期性离心力,进而引发机械振动。根据动力学原理,这种振动与转速平方成正比,在临界转速附近表现得尤为明显。复杂工况下的特殊性在于,工作参数的变化会导致系统动力学特性发生改变,传统静态平衡方法往往难以满足要求。
在精准控制策略方面,现代飞轮平衡机普遍采用自适应控制系统。这类系统通过实时监测振动信号,自动调整平衡参数。具体而言,系统包含三个关键环节:振动信号采集、不平衡量计算和校正执行。振动传感器通常采用高精度加速度计,布置在轴承座关键位置,采样频率需达到转速的10倍以上以保证数据可靠性。信号处理环节采用数字滤波技术,有效分离出与转速同频的振动分量。
针对复杂工况的特点,先进的控制算法显得尤为重要。模糊PID控制是目前较为成熟的解决方案,它将传统PID控制与模糊逻辑相结合,能够根据工况变化自动调整控制参数。实践表明,在转速波动±15%的工况下,采用模糊PID控制的系统平衡精度可比常规PID提高40%以上。基于模型预测控制(MPC)的方法也逐渐得到应用,其优势在于能够提前预测系统状态变化,特别适合处理存在时变特性的工况。
振动抑制方法可分为被动控制和主动控制两大类。被动控制主要依靠优化机械结构,如采用弹性支承、阻尼减振器等。这类方法可靠性高,但调节范围有限。主动控制则通过作动器产生反向振动来抵消不平衡力,具有更好的适应性。目前较为先进的方案是电磁主动平衡系统,它利用电磁力实时调整平衡状态,响应时间可控制在毫秒级。
在具体实施过程中,需要特别注意几个技术细节:一是相位测量的准确性,这直接影响平衡校正的效果。现代系统多采用数字编码器配合软件鉴相算法,相位识别精度可达±0.5°。二是校正质量的精确施加,对于可拆卸式飞轮可采用钻孔去重法,误差控制在0.1g以内;对于不可拆卸的场合,则需使用自动平衡头等在线校正装置。
系统集成方面,建议采用模块化设计思路。将测量模块、控制模块和执行模块相对独立,通过标准接口互联。这种架构不仅便于维护升级,还能根据具体需求灵活配置。例如,在高温环境下,可将信号采集模块移至温度较低区域,通过延长电缆连接传感器,有效避免电子元器件性能退化。
从实际应用效果来看,某型号航空发动机飞轮采用上述技术方案后,在转速3000-8000r/min范围内,振动烈度控制在1.2mm/s以下,比传统方法降低约60%。类似的,某大型水轮发电机组飞轮经过精密平衡后,轴承寿命延长了3倍以上。这些案例充分证明了先进平衡技术的重要价值。
展望未来,飞轮平衡技术将朝着智能化方向发展。基于深度学习的故障预测系统可以提前识别潜在的不平衡趋势;数字孪生技术能够实现虚拟调试和优化;5G技术的应用使得远程监控和诊断成为可能。这些新技术的融合应用,将进一步提升复杂工况下飞轮平衡的精度和效率。
复杂工况下的飞轮平衡是一个系统工程,需要综合运用精密测量、智能控制和先进振动抑制等技术手段。通过持续优化控制策略和方法,不仅可以提高设备运行稳定性,还能显著降低维护成本,为工业生产创造更大价值。