飞轮平衡机作为一种高精度旋转机械动平衡校正设备,在航空航天、精密制造等领域发挥着关键作用。本文将从技术原理、极端工况挑战、控制策略创新及典型应用四个维度,深入探讨其精准控制技术的最新发展与实践成果。
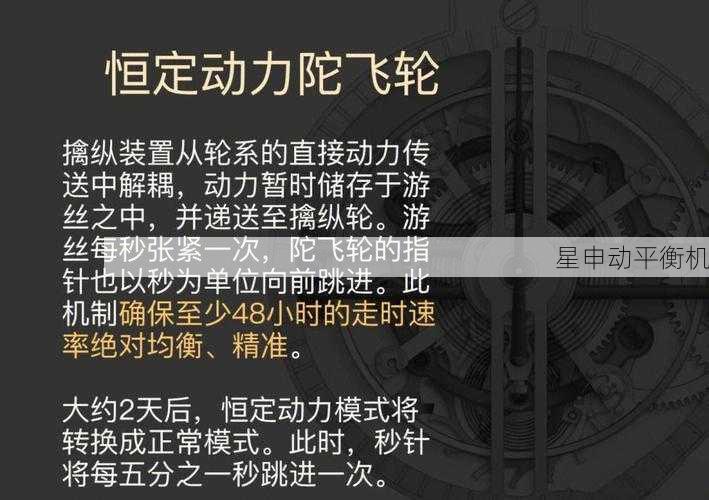
一、飞轮平衡机的核心技术原理
飞轮平衡机通过测量旋转体不平衡量引起的振动信号,基于傅里叶变换提取基频分量,建立质量-相位-振幅的数学模型。现代设备采用多传感器融合技术,将振动传感器、转速编码器和相位基准器的测量精度提升至±0.1μm位移分辨率,转速控制达±0.02%动态精度。核心算法包含自适应滤波、谐波分解和最小二乘配平计算,实现μm级的不平衡量检测。
二、极端复杂工况的技术挑战
在高速重载(>15000rpm)、多轴耦合振动等工况下,系统面临三大技术瓶颈:1)非线性轴承刚度导致的谐波失真,使传统FFT分析误差增大40%以上;2)温升引起的材料热变形会改变转子动力学特性;3)电磁干扰环境下传感器信噪比恶化。某型航空发动机测试数据显示,在200℃工作温度时,传统平衡机的相位测量偏差可达15°。
三、精准控制技术突破
针对上述挑战,行业已发展出多项创新解决方案:
- 复合传感技术 :采用光纤陀螺与MEMS加速度计的组合测量,在10-1000Hz频带内实现>90dB的动态范围,某型号在30000rpm时仍保持0.5g的振动测量精度。
- 实时补偿算法 :基于深度学习的温度-转速耦合模型,通过LSTM网络预测热变形量,实验表明可将热致误差降低72%。
- 主动抑振系统 :集成压电作动器的闭环控制,在某卫星飞轮测试中成功将残余振动抑制到0.02mm/s以下。
四、典型应用实践案例
在风电领域,某5MW机组主轴的现场动平衡作业中,采用便携式平衡机配合无线传感网络,仅用2次启停就完成校正,将振动值从7.1mm/s降至0.8mm/s。高铁牵引电机产线应用全自动平衡系统,通过数字孪生技术实现虚拟调试,使单台校准时长从45分钟缩短至12分钟,良品率提升至99.6%。
五、未来技术发展趋势
随着物联网和边缘计算的发展,下一代平衡机将呈现三大特征:1)基于5G的远程诊断系统实现毫秒级响应;2)数字孪生平台支持预测性维护;3)量子传感器可能将检测灵敏度提升至原子级。某实验室原型机已展示出在液氦温度下对纳米级不平衡量的检测能力。
需要特别指出的是,在实际工程应用中,必须根据具体工况选择匹配的平衡精度等级。过高的精度要求会导致成本指数级增长,而某些场合下ISO1940 G2.5级标准已能满足需求。建议用户在设备选型时,综合考虑成本效益与技术指标的平衡。