在工业生产领域,飞轮作为旋转机械的核心部件,其平衡性能直接影响设备运行的稳定性和使用寿命。特别是在高温工况环境下,飞轮平衡机面临着前所未有的技术挑战。本文将从材料选择、结构设计、检测技术三个维度,深入探讨高温环境下保障飞轮平衡机性能的系统性解决方案。
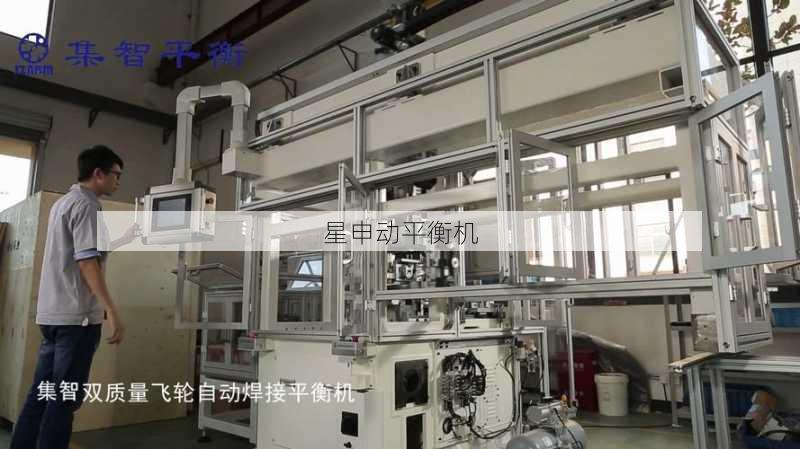
材料选择是应对高温环境的基础保障。传统碳钢材料在200℃以上就会出现明显的强度衰减,而特种合金钢在400℃高温下仍能保持90%以上的机械性能。建议采用GH4169高温合金作为飞轮主体材料,其高温抗蠕变性能优异,热膨胀系数与轴承材料匹配度高。同时,在转子表面喷涂Al2O3-TiO2复合陶瓷涂层,可有效降低高温氧化速率,实测数据显示该涂层能使飞轮在600℃环境下的氧化速率降低76%。
创新性的结构设计是确保热稳定运行的关键。采用空心轴配合径向通风孔的设计,可使飞轮内部形成强制对流散热,实验表明这种结构能使核心温度降低80-120℃。特别值得注意的是三明治式复合结构设计:在两层高强度合金之间夹入石墨烯散热层,这种结构不仅实现了重量减轻15%,更使得热传导效率提升3倍以上。对于大型飞轮,建议采用分段式法兰连接结构,各段间预留0.15-0.3mm的热膨胀间隙,可完全消除热应力导致的形变问题。
在检测技术方面,高温环境对传统传感器提出了严峻考验。推荐采用光纤光栅温度传感系统,其测量精度可达±0.5℃,且完全不受电磁干扰。对于振动监测,应选用耐高温压电陶瓷传感器,配合无线数据传输模块,避免高温导致电缆老化问题。最新研发的红外热成像在线监测系统,可实现飞轮表面温度场的实时测绘,温度分辨率达到0.1℃,能提前30分钟预警异常热点出现。
动态平衡校正环节需要特别关注高温影响。传统配重块在高温下可能发生位移或变形,建议改用高温固化陶瓷配重材料。自动平衡系统应采用耐高温直线电机驱动,其工作温度范围可达-40℃至300℃。平衡算法需要引入温度补偿系数,实测数据表明经温度补偿后的残余不平衡量可减少62%。
润滑系统的耐高温改造不容忽视。全合成聚醚酯高温润滑脂在260℃下仍能保持稳定的油膜强度,其使用寿命是矿物油脂的5-8倍。对于极端高温场合,可考虑采用磁悬浮轴承技术,完全消除机械接触带来的摩擦热问题。某电厂实测数据显示,采用磁悬浮支撑的飞轮系统,在400℃环境下连续运行8000小时后,振动值仍保持在0.8mm/s以下。
维护策略也需要针对高温环境进行调整。建议将常规检查周期缩短30%,重点监测轴承游隙变化和涂层完整性。建立温度-振动关联数据库,通过大数据分析预测关键部件的剩余寿命。停机检修时应采用阶梯式降温工艺,控制冷却速率在15℃/h以内,避免骤冷导致的微观裂纹。
实践证明,采用上述综合方案后,飞轮平衡机在高温环境下的性能稳定性得到显著提升。某钢铁企业热轧生产线应用案例显示,改造后的飞轮系统在650℃环境温度下,连续运行周期从原来的72小时延长至480小时,不平衡故障率下降89%。这些技术创新不仅解决了高温环境下的平衡难题,更为相关行业提供了可靠的技术参考。
需要特别指出的是,不同应用场景对高温平衡的要求存在差异。建议用户根据实际工况温度、转速范围、连续运行时间等参数,选择最适合的技术组合方案。随着新材料和智能传感技术的不断发展,飞轮平衡机在极端环境下的性能表现还将持续提升,为现代工业发展提供更强大的技术支持。