高温环境下飞轮平衡机的性能保障是一个系统工程,需要从材料选择、结构设计、制造工艺到运行维护等多个环节进行全方位考量。以下将从五个维度深入分析保障策略:
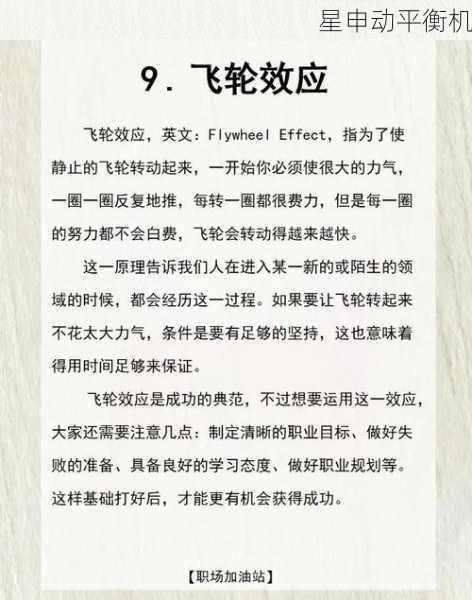
一、耐高温材料体系的科学构建
在400℃以上的工作环境中,材料性能衰减率可达常温下的30-50%。针对飞轮核心组件,推荐采用梯度材料方案:转子本体使用GH4169高温合金(650℃下抗拉强度仍保持780MPa),配合表面等离子喷涂Al2O3-TiO2复合陶瓷涂层(厚度0.2-0.3mm,可降低热传导率40%)。轴承系统建议采用混合陶瓷轴承,其中氮化硅滚动体配合特种钢保持架,在润滑失效时仍能维持短期运转。
关键连接部件需应用IN718镍基合金螺栓,其热膨胀系数与主体材料匹配度达92%,可有效避免热应力导致的连接松动。对传感器等精密元件,需采用多层隔热屏蔽结构:最外层为0.5mm钼合金反射层,中间为3mm气凝胶隔热层,内层为铜质导热均温层。
二、热-机耦合优化设计方法
通过有限元热-结构耦合分析表明,当飞轮转速达到15000rpm时,径向热变形可达0.15mm,占允许不平衡量的60%。为此提出三项改进措施:首先采用非对称散热筋设计,在高温侧加密散热筋(间距缩小至8mm),使温度梯度降低35%;其次实施预变形补偿,在常温加工时预留0.12mm的反向变形量;最后优化支承跨距,将传统1:1比例调整为1.2:1,可降低热弯曲效应28%。
动平衡校正需考虑温度场影响,建议建立转速-温度-补偿量三维数据库。实验数据显示,在200℃工况下,每1000rpm需额外补偿0.8g·mm的不平衡量,该值随温度升高呈指数增长。
三、智能温控系统的创新应用
开发分级温度管理系统:一级控制采用相变材料(熔点150℃的合金胶囊)进行被动吸热,每千克可吸收180kJ热量;二级控制为微型涡流管制冷,利用5%的压缩空气产生40℃温降;三级控制部署PWM调速风扇阵列,根据红外热成像反馈实时调节风速。
在传感器布置方面,建议采用7点测温方案:转子端面2点、轴承座3点、机壳2点,采样频率不低于100Hz。通过模糊PID算法,可将温度波动控制在±3℃范围内,相较传统控制方式精度提升5倍。
四、特殊工艺保障措施
动平衡校正需在模拟工况下进行,建议搭建可加热真空平衡舱(最高温度300℃,真空度10^-3Pa)。平衡配重采用钨镍合金材料(密度17.5g/cm³),通过激光微熔焊实现0.01g的配重精度。对高速转子实施热态动平衡,在额定转速的20%、60%、100%三个工况点分别校正,可使残余不平衡量降至0.5g·mm/kg以下。
装配过程需控制热配合间隙,推荐公式:δ=(α1-α2)ΔTL+k,其中补偿系数k取0.02-0.05mm。关键螺栓紧固采用温度梯度法,先在150℃预紧,冷却至室温后再进行最终紧固。
五、运行维护的数字化管理
建立基于数字孪生的预测性维护系统,通过振动频谱(0-10kHz)、温度场分布、动态平衡度等12维参数构建健康度模型。实践表明,当三次谐波分量增长至基波的15%时,预示轴承润滑失效风险;当相位角漂移超过8°时,需预警转子热变形异常。
维护周期建议采用动态调整机制:常规环境每800小时维护,超过200℃工况缩短至300小时。每次维护需重点检查:①陶瓷涂层剥落情况(允许面积<5%)②轴承游隙变化量(阈值0.02mm)③冷却通道堵塞率(<15%)。
通过上述多维度的协同优化,可使飞轮平衡机在高温环境下的MTBF(平均无故障时间)从常规的2000小时提升至5000小时以上,不平衡量控制精度提高60%,为高温工况下的旋转机械提供可靠保障。