飞轮平衡机作为精密机械制造领域的重要设备,在多轴联动系统中发挥着不可替代的作用。本文将从工作原理、协调机制和关键技术三个维度,深入分析飞轮平衡机在多轴联动环境中的核心价值。
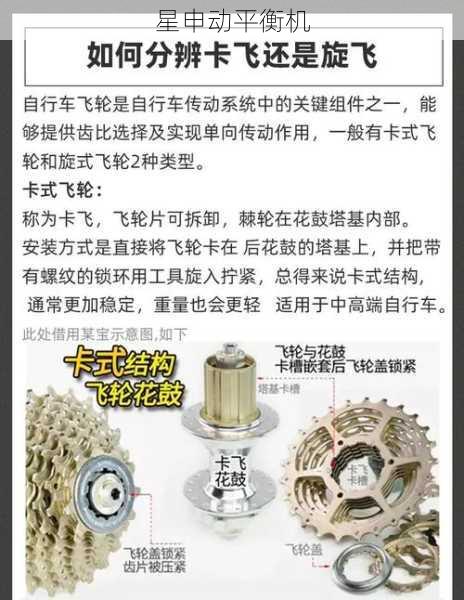
从基本原理来看,飞轮平衡机通过检测旋转部件的质量分布不均,利用配重补偿或材料去除的方式实现动平衡。在多轴联动场景下,这种平衡作用呈现出更复杂的特性。当多个旋转轴同时工作时,各轴系的振动会相互耦合,形成复杂的谐波干扰。飞轮平衡机此时不仅要解决单轴平衡问题,更需要协调各轴系之间的动态相互作用。
在协调作用方面,现代飞轮平衡机主要体现三大功能:首先是相位同步控制,通过高精度编码器实时监测各轴相位差,确保多轴转动时振动波峰波谷相互抵消;其次是动态刚度匹配,根据各轴负载特性自动调整平衡参数,避免共振放大效应;最后是谐波抑制功能,通过FFT频谱分析识别并消除轴系间的谐波干扰。
关键技术层面,多轴联动对飞轮平衡机提出了更高要求。传感器融合技术是基础保障,需要将振动传感器、转速传感器和位置传感器的数据进行卡尔曼滤波融合,提高测量精度。自适应算法是核心突破,现代平衡机普遍采用模糊PID控制,能根据转速变化自动调整控制参数。数字孪生技术是前沿方向,通过建立虚拟样机实现平衡参数的预调试。
在实际应用中,这些技术协同工作形成完整的解决方案。以某五轴加工中心为例,其主轴转速达20000rpm时,采用多传感器融合技术可将振动检测精度控制在0.1μm以内;自适应算法使平衡调整时间缩短至传统方法的1/3;数字孪生技术则能提前预测不同加工参数下的振动特性,实现预防性平衡。
值得注意的是,多轴联动环境下的平衡效果评价标准也更为复杂。除了常规的振动幅值指标外,还需要考虑轴间耦合度、相位一致性等参数。这要求平衡机具备多维数据分析能力,现代设备通常集成专业分析软件,可生成三维振动云图和谐波矩阵等可视化报告。
维护保养方面,多轴系统中的飞轮平衡机需要特别关注传感器校准和算法优化。建议每500工作小时进行基准校验,每2000工作小时更新控制参数库。同时要注意环境温湿度变化对测量精度的影响,保持工作环境温度波动在±2℃范围内。
展望未来,随着工业4.0的发展,飞轮平衡机将向智能化方向发展。基于深度学习的预测性维护、5G远程监控等新技术将进一步提升多轴联动系统的平衡性能。特别是在高速精密加工、航空航天等领域,对多轴协调平衡的需求将持续推动技术创新。
飞轮平衡机在多轴联动系统中扮演着振动协调者的关键角色。通过先进传感技术、智能算法和数字孪生等技术的综合应用,有效解决了多轴耦合振动这一行业难题,为高端装备制造提供了重要的技术支撑。