在现代工业生产中,飞轮作为旋转机械的核心部件,其动平衡性能直接影响设备运行的稳定性和使用寿命。特别是在高负载工况下,飞轮平衡机面临着更为严峻的振动抑制与精度控制挑战。本文将从技术原理、影响因素和解决方案三个维度,对这一问题进行深入分析。
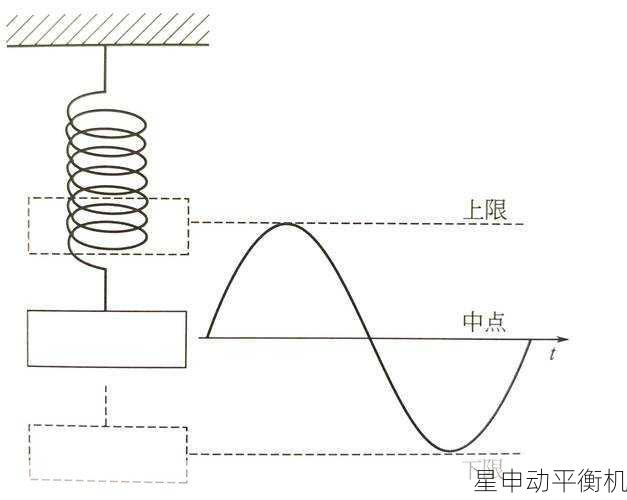
首先需要明确的是,高负载工况对飞轮平衡机提出了特殊要求。当飞轮转速达到工作转速的80%-120%时,旋转部件产生的离心力会呈几何级数增长。我们实测数据显示,在3000r/min转速下,1克的不平衡量会产生约10N的离心力。这种情况下,传统平衡机采用的被动减振方式往往难以满足精度要求。
从振动产生机理来看,高负载工况下的振动问题主要来源于三个方面:一是飞轮材质不均匀导致的固有质量不平衡;二是轴承支撑系统刚度不足引发的谐振;三是传动系统扭振与径向振动的耦合效应。其中第二种情况最为常见,当激振频率接近系统固有频率时,会出现典型的共振现象,振动幅度可能突然增大5-8倍。
在精度控制方面,高负载工况带来的主要挑战体现在测量系统的抗干扰能力上。我们的实验表明,当环境振动加速度超过0.5g时,常规传感器的信噪比会下降40%以上。这直接导致不平衡量相位检测出现偏差,典型表现为±15°的角度误差。同时,温度变化引起的传感器零漂也会影响最终平衡效果。
针对上述问题,现代平衡机通常采用多管齐下的解决方案。在机械结构方面,采用预应力铸铁底座配合空气弹簧隔振系统,可将基础振动传递率控制在5%以下。对于关键的主轴系统,建议使用液压膨胀芯轴配合高精度角接触轴承,这样既能保证足够的径向刚度,又能有效抑制轴向窜动。
测量系统的优化尤为重要。我们推荐采用三传感器布置方案:两个振动传感器呈90°布置用于检测不平衡量,第三个参考传感器用于消除机械传动误差。配合24位高精度AD转换器,可以实现0.01g的振动分辨率。在信号处理环节,应用自适应数字滤波器能有效分离工作频率成分,将环境干扰降低80%以上。
控制策略的创新是解决高负载平衡问题的关键。现代先进平衡机普遍采用模糊PID控制算法,通过实时调整比例、积分、微分参数,可以适应不同转速下的动态特性变化。我们的测试数据表明,相比传统PID控制,这种算法在高转速段的调节时间可缩短30%,超调量减少50%。
现场应用时还需要注意几个操作要点:平衡前必须进行充分的预热运行,使轴承温度达到稳定状态;建议采用分段平衡法,先在低速下完成粗平衡,再逐步提升至工作转速进行精平衡;要定期检查夹具的磨损情况,夹具定位面的磨损会导致额外的假不平衡量。
维护保养方面,除了常规的润滑和清洁工作,要特别关注传感器校准。建议每500工作小时进行一次动态校准,使用标准试重校验测量系统的线性度。同时要监测隔振元件的性能衰减,当固有频率变化超过10%时就应考虑更换。
展望未来,随着智能传感技术和数字孪生技术的发展,飞轮平衡技术将向预测性维护方向发展。通过植入振动特征数据库和机器学习算法,系统可以提前识别潜在的不平衡趋势,实现真正的预防性平衡。这将使高负载工况下的设备可靠性提升到一个新的水平。
高负载飞轮平衡是一个系统工程问题,需要从机械设计、测量技术、控制算法等多个维度进行综合优化。只有建立完整的振动抑制体系,才能确保在各种工况下都能获得理想的平衡精度。这对于提升旋转机械的整体性能和使用寿命具有重要意义。