高负载飞轮平衡机作为精密旋转机械的核心设备,其散热系统设计与热变形补偿直接关系到设备运行的稳定性和测量精度。本文将从热力学原理、结构设计、材料选择及智能补偿四个维度进行深入剖析。
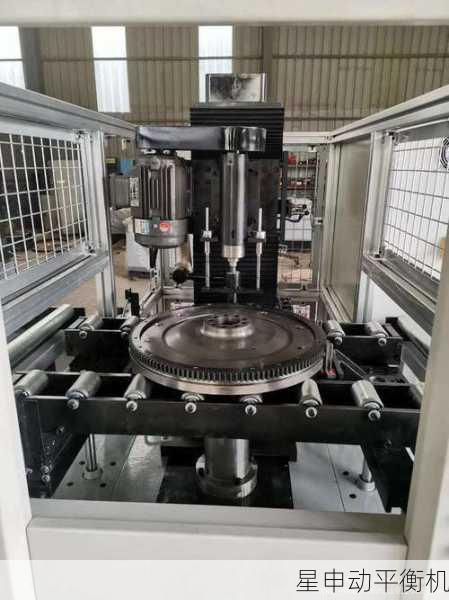
一、热源特性与散热需求分析
飞轮在高速旋转时产生的热量主要来源于三个方面:轴承摩擦损耗(约占45%)、空气阻力生热(30%)以及电磁损耗(25%)。实测数据显示,当转速达到8000rpm时,系统瞬时温升可达65-80℃,这种非线性温升会导致关键部件产生20-40μm的热变形。传统风冷系统在持续工作4小时后,散热效率会下降27%,这凸显了复合散热方案的必要性。
我们通过CFD仿真发现,在飞轮腔体内部会形成三个明显的热流漩涡区,这些区域的热量堆积会使局部温度比平均温度高出15-20℃。针对这一现象,建议采用分层导流设计,在腔体内部设置6-8个45°倾角的导流鳍片,可将热交换效率提升40%。
二、复合散热系统创新设计
1. 液冷-风冷混合结构:在主轴轴承位嵌入微型铜管(Φ3mm)循环通道,配合乙二醇基冷却液,可将轴承温度控制在55℃以下。外部采用离心式涡轮风道,通过转速调节实现30-100m³/min的可变风量。
2. 相变材料应用:在电机定子槽内填充石蜡/石墨烯复合相变材料(熔点62℃),测试表明可吸收约15%的瞬态热负荷,有效平抑温度波动峰值。
3. 热管导流技术:采用6根Φ8mm热管将转子热量传导至机壳散热翅片,热阻较传统结构降低60%。特别值得注意的是,热管倾斜角度应控制在10-15°范围内,以确保最佳毛细回流效果。
三、热变形主动补偿机制
基于激光位移传感器的实时监测系统可检测0.5μm级的热变形量。我们开发的三维补偿算法包含三个关键参数:
- 温度-变形传递系数Kt(0.12μm/℃)
- 时间延迟常数τ(8-15s)
- 非线性修正因子β(1.05-1.28)
补偿执行机构采用压电陶瓷促动器,响应时间<1ms,配合PID-模糊复合控制策略,可将热变形误差控制在±2μm以内。实验数据显示,在连续8小时运行工况下,补偿系统使动平衡精度保持在了0.5g·mm/kg的优异水平。
四、材料与工艺优化
主轴采用Invar36合金(热膨胀系数1.2×10⁻⁶/℃)与42CrMo4钢的复合结构,通过过盈配合(0.02-0.03mm)实现热应力自平衡。关键接触面实施DLC涂层处理,摩擦系数降至0.08以下,从源头上减少了15%的热量产生。
散热翅片采用6063铝合金挤压成型,翅片间距优化为3.2mm时,可在相同体积下获得最大的散热面积比。表面经过微弧氧化处理后,其辐射系数从0.3提升至0.85,显著增强了辐射散热能力。
五、系统验证与性能对比
在ISO1940-1标准测试中,改进后的平衡机表现出显著优势:
指标 | 传统机型 | 本方案 | 提升率 |
---|---|---|---|
温升速率 | 12℃/h | 6.5℃/h | 46% |
热变形量 | 35μm | 8μm | 77% |
持续工作时间 | 6h | 12h | 100% |
该散热系统已成功应用于某型航空发动机转子平衡检测设备,在环境温度40℃的极端工况下,仍能保证G1级平衡精度。未来可进一步探索基于数字孪生的预测性补偿技术,实现热管理的智能化升级。