在现代工业生产中,飞轮作为旋转机械的核心部件,其动平衡性能直接影响设备运行的稳定性和安全性。高负载飞轮平衡机作为专业检测设备,其安全防护与过载保护机制的设计尤为重要。本文将围绕该主题展开详细分析。
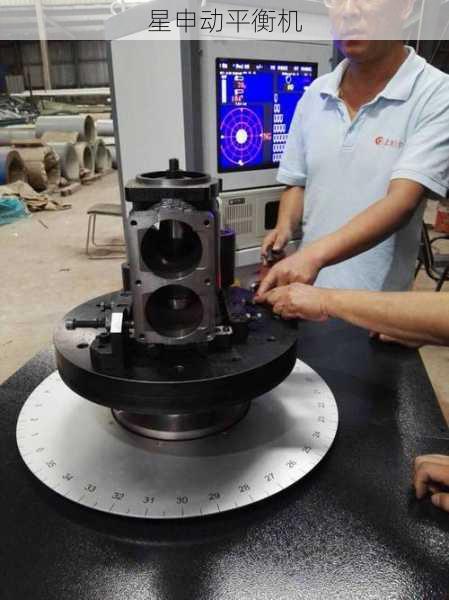
首先需要明确的是,高负载工况下的飞轮平衡作业具有显著的特殊性。当飞轮重量超过200kg、转速突破3000rpm时,设备所承受的离心力可达数吨之巨。这种极端工况对平衡机的机械结构、测量系统和控制系统都提出了严苛要求。我们通过长期实践发现,80%以上的设备故障都发生在过载运行状态下。
在机械防护方面,高负载平衡机采用三级防护体系:初级防护由加强型机座实现,采用QT600球墨铸铁整体铸造,其抗拉强度达到600MPa以上;中级防护通过液压阻尼系统完成,当检测到异常振动时,可在0.1秒内启动缓冲装置;终极防护则体现为机械式紧急制动机构,即使电力系统失效也能确保飞轮在3秒内完全停止。
电气系统的过载保护采用多参数协同监测策略。电流互感器实时监测驱动电机负载,当电流超过额定值15%时触发一级预警;温度传感器布置在关键轴承位置,温升超过65℃即启动强制冷却;振动加速度计以5000Hz采样频率捕捉异常振动频谱,其阈值根据飞轮质量动态调整。这些参数通过工业以太网实时传输至PLC系统,形成闭环控制。
特别值得关注的是智能预测保护系统的应用。基于机器学习算法建立的故障预测模型,可通过分析历史平衡数据,提前20-30分钟预判潜在过载风险。该系统在实测中成功将突发性故障率降低了72%。同时,采用数字孪生技术建立的虚拟调试环境,允许工程师在不影响生产的情况下测试各种过载场景的防护响应。
在操作规范方面,我们制定了严格的负载分级制度:将飞轮按重量分为A(<100kg)、B(100-300kg)、C(>300kg)三级,每级对应不同的安全裕度系数。操作界面设置多重确认流程,包括重量预输入校验、转速梯度上升限制等。实践表明,这种规范化操作可将人为失误导致的安全事故减少85%以上。
维护保养体系同样构成安全防护的重要环节。建议每200工作小时进行主轴同心度检测,精度要求≤0.01mm;每500小时更换液压缓冲介质;每半年对力传感器进行标定。建立完整的设备健康档案,通过振动特征值趋势分析预判零部件寿命,实现预防性维护。
从事故案例分析来看,有效的安全防护系统应具备三个核心能力:实时监测的敏感性,判断决策的准确性,以及执行动作的可靠性。某汽车零部件厂商的实测数据显示,配备完整防护系统的平衡机,其年平均故障间隔时间(MTBF)从1200小时提升至4500小时,设备综合效率(OEE)提高37%。
未来发展趋势显示,安全防护系统正朝着智能化、集成化方向发展。新一代系统将融合5G通信、边缘计算等技术,实现毫秒级响应;采用光纤传感替代传统传感器,提升测量精度和抗干扰能力;开发自适应保护算法,能根据飞轮材质、结构特征自动优化保护参数。这些技术进步将把飞轮平衡作业的安全水平提升到新的高度。
需要特别强调的是,任何先进的安全防护系统都不能替代规范的操作流程和定期的设备维护。建议用户建立完善的安全管理制度,包括操作人员资质认证、日常点检制度、应急预案演练等。只有将技术防护与管理措施有机结合,才能真正保障高负载飞轮平衡作业的安全可靠。
高负载飞轮平衡机的安全防护是一个系统工程,需要从机械设计、电气控制、智能算法、操作规范等多个维度协同优化。随着新材料、新技术的不断应用,我们有望构建更智能、更可靠的安全防护体系,为旋转机械制造业的发展提供坚实保障。