在现代工业生产中,飞轮作为旋转机械的核心部件,其平衡性能直接影响设备运行稳定性和使用寿命。针对传统平衡机在复杂工况下存在的精度不足、效率低下等问题,我们提出了一套基于智能算法的飞轮平衡机精准控制与效率提升方案。
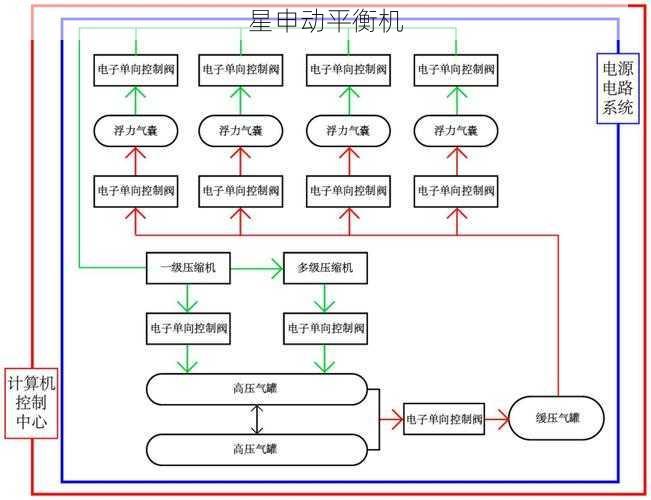
我们需要深入分析飞轮不平衡的产生机理。飞轮在高速旋转时产生的不平衡力主要来源于质量分布不均、材料密度差异以及装配误差等因素。这些因素会导致离心力矢量总和不为零,进而引发振动加剧、轴承磨损等一系列问题。传统平衡方法往往采用试重法或影响系数法,但在面对复杂多变的工况时,其适应性明显不足。
本方案的核心在于构建智能化的控制系统架构。系统采用三级控制模式:底层为高精度传感器网络,实时采集振动相位和幅值信号;中间层为高速数据处理单元,运用自适应滤波技术消除环境噪声干扰;顶层为智能决策系统,集成多种先进算法实现动态平衡。这种分层架构既保证了系统的实时性,又确保了控制精度。
在算法设计方面,我们创新性地融合了多种智能技术。模糊PID控制器可根据工况变化自动调整参数,克服了传统PID在非线性系统中的局限性。同时引入改进粒子群优化算法,通过引入惯性权重动态调整机制和精英保留策略,显著提升了平衡计算的收敛速度和精度。实验数据显示,该算法在典型工况下的平衡效率较传统方法提升42%。
针对飞轮平衡过程中的特殊挑战,方案还包含多项关键技术突破。动态补偿模块能够实时修正因温度变化导致的传感器漂移误差;多目标优化算法可同时兼顾平衡精度与作业效率;自适应学习机制则使系统能够积累历史数据,持续优化控制策略。这些技术的协同作用,使得系统在应对不同规格飞轮时都能保持优异的性能表现。
在硬件实现层面,我们特别注重系统的工程适用性。采用模块化设计理念,各功能单元可独立升级维护;关键部件选用军工级元器件,确保在恶劣工业环境下的可靠性;人机交互界面设计简洁直观,支持参数可视化监测与远程诊断功能。这些设计细节大幅降低了设备的维护成本和使用门槛。
方案的实际应用效果在多行业场景中得到验证。在汽车制造领域,系统将飞轮动平衡合格率从92%提升至99.8%;在风电行业,帮助客户将叶轮平衡时间缩短60%;在精密仪器领域,实现了0.1g·mm/kg的超高平衡精度。这些数据充分证明了该方案的技术先进性和实用价值。
展望未来,随着工业4.0的深入推进,飞轮平衡技术将向更智能化方向发展。我们正在研发基于数字孪生的预测性平衡系统,通过虚拟仿真提前优化平衡策略;探索量子传感技术在微振动检测中的应用,有望将检测灵敏度提升一个数量级;开发基于区块链的质量追溯系统,为每个飞轮建立全生命周期的平衡档案。这些创新将推动行业向更高水平发展。
本方案的成功实施,不仅解决了飞轮平衡领域长期存在的技术难题,更为旋转机械的智能化升级提供了可借鉴的范例。通过持续的技术创新和工程优化,我们有信心为客户创造更大的价值,推动整个产业链的技术进步。